Mnoho pekáren po celém světě používá známou patentovanou glazuru jako náhradu vaječné polevy u velkoobjemových výrobků, jako jsou buchty. Obvykle se nanáší pomocí rozprašovacích trysek umístěných nad dopravníkem. V závodě ve Velké Británii, který provozuje jedna z největších pekárenských skupin v Evropě, se glazura nanáší nepřetržitě prostřednictvím jediné hydraulické trysky s plochým nástřikem VeeJet.
Při stříkání pod úhlem 90° směrem ven nad přepravkami s houskami, které byly přepravovány, docházelo ke značnému přestřiku, který pokrýval okolní povrchy do té míry, že bylo nutné použít záchytné vaničky. Každou hodinu během každé pracovní směny musel celý prostor postřiku čistit speciální úklidový tým.
Tento proces byl zjevně neekonomický a nákladný z hlediska materiálu i práce. V roce 2016 se pekárna rozhodla, že prioritou musí být snížení průběžných provozních nákladů, a proto začala hledat nový systém zasklívání.
Systém zasklívání pekárny
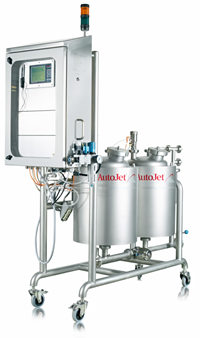
Cíle pekárny byly jednoduché: snížit množství stříkané glazury a zlepšit čistotu prostoru. Modulární řešení předložené společností Spraying Systems slibovalo obojí.
Návrh se týkal systému AutoJet® PHM AccuGlaze Egg Wash Coating System s řídicí jednotkou 2250+ PLC, v němž je glazura přiváděna ze dvou 50litrových nádrží s automatickým doplňováním do stříkacího ústrojí PulsaJet® se šesti tryskami. Systém využívá snímač a stříká pouze tehdy, když jsou housky pod tryskami. Všechny prvky systému, včetně vnějších, jako je rychlost dopravníku, jsou nepřetržitě monitorovány. Pokud se rychlost změní, průtok kapaliny se podle toho automaticky upraví.
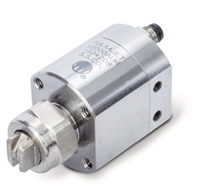
Samotné trysky PulsaJet® jsou u systému Spraying Systems jedinečné. Průtok, úhel rozstřiku a velikost kapek jsou nezávislé na tlaku v potrubí. Průtok se mění opakovaným velmi rychlým zapínáním a vypínáním trysky (až tisíce cyklů za minutu). Procento doby "zapnutí" (proměnné od nuly do 100 %) určuje objem vystříknuté kapaliny za jednotku času. Spád jedné trysky nebo hlavice PulsaJet® je plně flexibilní a trysky není nutné vybírat pouze podle průtoku.
Aby si zákazník ověřil výkonnost postřiku a očekávání snížení spotřeby glazury, rozhodl se před zadáním objednávky pro zkušební provoz na místě. O šest týdnů později byly zakoupeny a nainstalovány dva systémy.
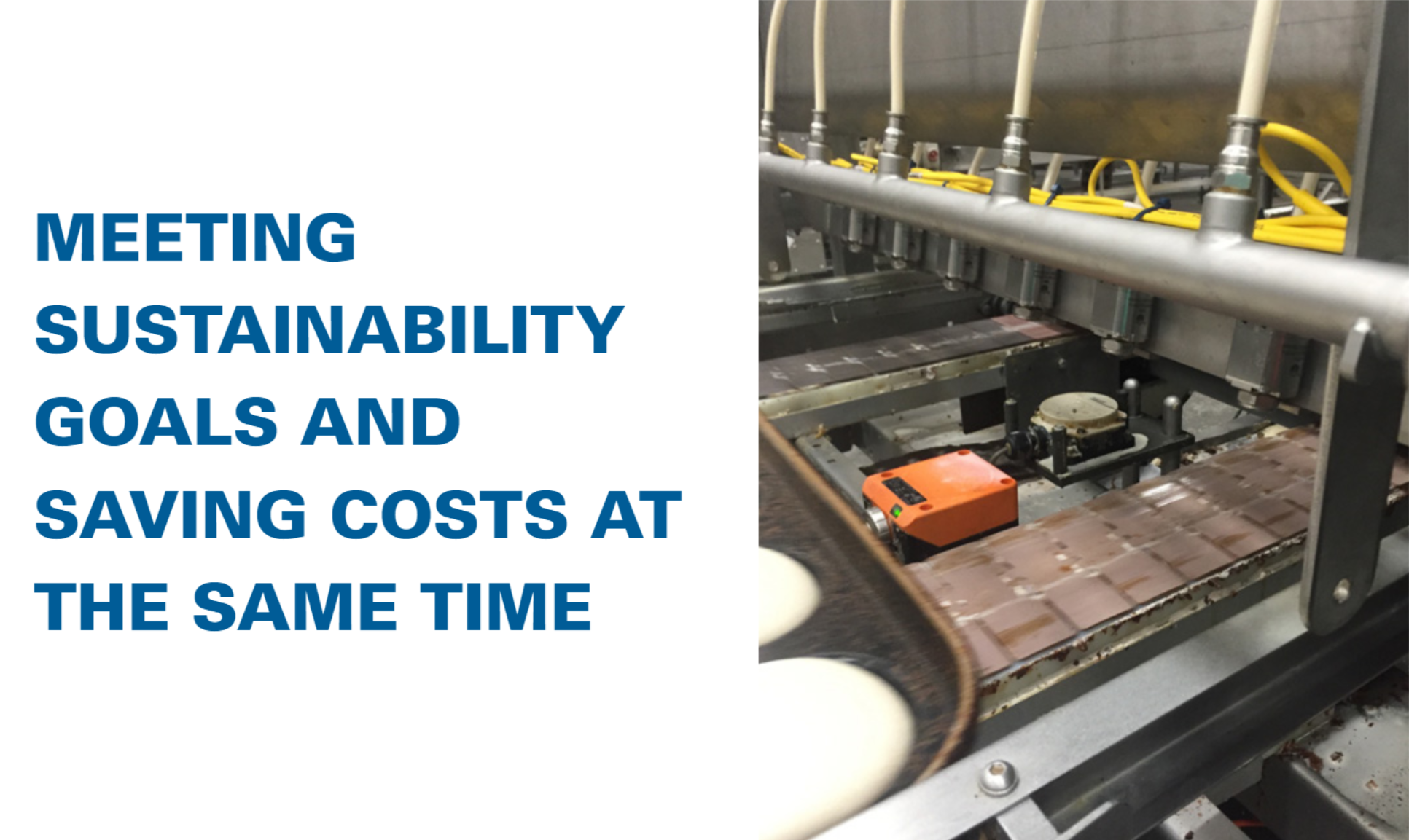
Výsledek
Zákazník spotřeboval patentovanou glazuru v množství více než 40 litrů za hodinu. Se systémem AutoJet® se spotřeba glazury snížila na méně než 8 litrů/hod. Nyní již není nutné provádět čištění během směny. Veškerá glazura se nanáší na housky s velmi malým množstvím přestřiku. Za méně než 3 měsíce dosáhla pekárna plné návratnosti obou zakoupených systémů. S tím souvisí další výhody. Glazura se před použitím uchovává v chladu.
Nyní se snižuje objem uchovávané hmoty, což znamená, že se snižují i náklady na energii potřebnou k chlazení. Hodinové čištění bylo náročné na spotřebu vody. Čištění pouze jednou, na konci směny, šetří vodu. Zákazník rovněž zaznamenal zlepšení v oblasti bezpečnosti a ochrany zdraví. U předchozího systému představovala přestříkaná glazura padající kolem místa stříkání potenciální nebezpečí uklouznutí, které bylo nyní odstraněno.