Beverage Can Manufacturer Doubles Chain Life on Pin Conveyor and Eliminates Customer Complaints
Beverage Can Manufacturer Doubles Chain Life on Pin Conveyor and Eliminates Customer Complaints
Problem:
KJM Aluminium Can, a part of the Kian Joo Group and Malaysia’s largest can manufacturer, wanted to improve the lubrication system on a can conveyor. KJM also needed to eliminate oil contamination in two-piece aluminum beverage cans and extend pin oven chain life. KJM previously used an air-assisted lubrication system on the conveyor chain leading into the pin oven where the protective lacquer coating is cured. The system used excessive oil and required re-tensioning of the chain every other month resulting in a chain life of only six months – all costly problems. The most serious problem was the oil mist created by the system. The oil mist contaminated the internal surface of the cans and prevented the lacquer coating from adhering and curing properly. This led to corrosion in the beverage cans after filling and caused numerous customer complaints.
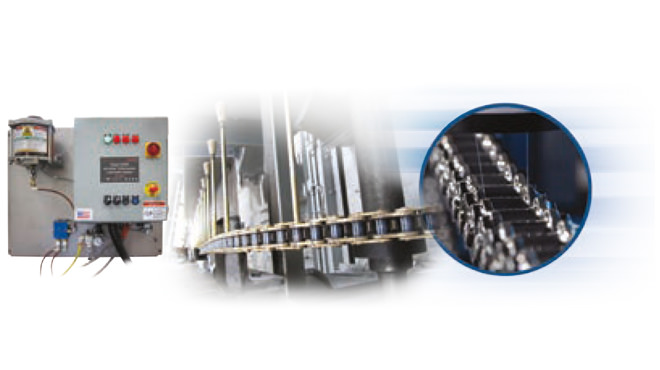
Solution:
Spraying Systems Co.’s solution uses electrostatic spray technology to meet KJM’s challenges. Operation of the AutoJet® Electrostatic Chain Lube System is simple and straightforward. The AutoJet Spray Controller included with the system controls the flow of oil to two electrostatic nozzles which apply oil to key lubrication points on the chain. Each nozzle is supplied by a low-flow injector pump and can be controlled independently. A system alarm notifies operators when the oil level in the 16 liter (4.2 gallon) reservoir is low. Electrostatic spraying produces extremely high transfer efficiency, so KJM’s previous oil mist problem has been eliminated.
Results:
The AutoJet® Electrostatic Chain Lube System has delivered dramatic results for KJM. Oil use has decreased by more than 50% and chain life has doubled from six to twelve months, saving more than US$12,000 annually. Better lubrication has enabled KJM to eliminate the downtime previously caused by re-tensioning the chain every other month and has also provided a 15% increase in production line speed, from 1300 to 1500 cans per minute. Most importantly, the electrostatic spray technology has eliminated misting and overspray along with customer complaints about corroded beverage cans.
For complete details of this case study click here to see the PDF version.