Modeling Helps Refinery Optimize Tank Mixing Operations
Modeling Helps Refinery Optimize Tank Mixing Operations
Problem:
A major refinery wanted to install a blending system in a 250,000 barrel petroleum storage tank. However, certain challenges had to be overcome to ensure effective blending. The density of the additives varied and the lower density solutions could rise to the top of the tank and vaporize if not properly blended with the gasoline. If vaporization occurred, the octane level would decrease and the gasoline could not be sold as premium grade – a considerable revenue loss for the refinery.
Another challenge was the floating roof on the tank, which was used to minimize thermal evaporation of the gasoline. Disturbances to the fuel surface had to be minimized in order to avoid causing any damage to the floating structure, which could cost hundreds of thousands of dollars to repair. Finally, the time required for complete blending had to be consistent to ensure that transportation of the fuel through the pipeline could be scheduled without any missed deliveries.
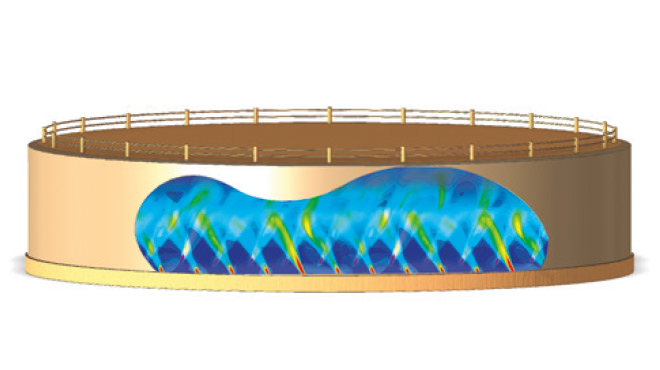
Solution:
Using Computational Fluid Dynamics (CFD) modeling, Spraying Systems Co. designed eductor headers to provide the required mixing in the least amount of time. The CFD modeling determined:
- The size and position of the header system in the tank
- The number, the size and the position of the eductors on the header system
- Blending effectiveness and flow velocity throughout the tank
- Turbulence throughout the tank to verify that damage to the floating roof could be avoided
A recirculation pump and 76 stainless steel tank mixing eductors mounted on a header system proved to be the most effective design. CFD modeling determined that four to six hours were required to ensure uniform mixing – a 99.95% reduction in Coefficient of Variation (CoV).
Low pressure pumps were used, minimizing the cost of the pumps and the ongoing operating costs. Low pressure piping was also used for the headers, providing additional savings.
Results:
The eductor system designed using CFD modeling was installed and has operated flawlessly, ensuring effective blending on time without damage to the floating roof. Considering the cost required to repair the floating roof of the tank, the potential loss of revenue for fuel that could not be sold as premium blend and the fees associated with late delivery, the payback on the CFD modeling study and the eductor system was immediate. The same system design was subsequently used for five additional blending tanks.
For complete details of this case study, click here to see the PDF version.