Lone Star Dairy Saves
Lone Star Dairy Saves
SV SprayDry® nozzles improve safety, reduce waste and increase annual revenue by more than US$2.5 million.
Problem:
ELIMINATE NOZZLE BEARDING AND CLOGGING TO ADDRESS SAFETY AND PRODUCTION CONCERNS
Lone Star Dairy Products, a leading producer of valueadded dairy ingredients, was experiencing problems related to its spray drying nozzles. Most critically, build-up or “bearding” of burned milk powder on the nozzles created the risk of dryer fires and explosions that could harm workers and damage equipment. In addition, clogging caused by external powder build-up and the design of the nozzle resulted in sporadic pressure changes, inconsistent particle size and wasted product. The nozzles also required frequent cleaning, cutting production runs short and reducing the volume of saleable powder.
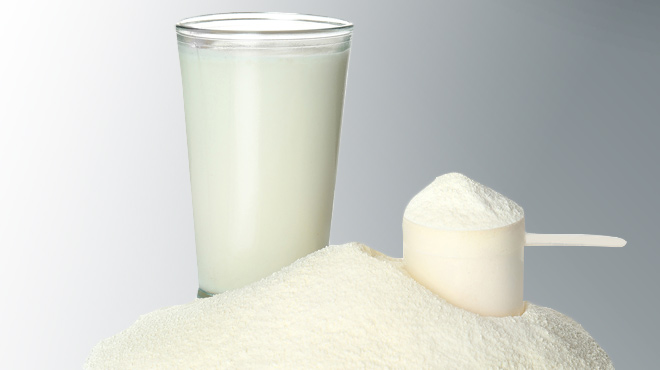
Solution:
SV SprayDry nozzles with anti-bearding caps were the ideal solution for two spray dryers at Lone Star Dairy Products. The anti-bearding feature minimizes build-up on the nozzle face during operation and the
one-piece swirlchambers have large free passages that have eliminated clogging. Swirlchambers and orifices are constructed from an engineered tungsten carbide which has greatly improved wear life. Finally, SV nozzles can be hand-tightened, which has minimized downtime when maintenance is required.
Results:
The SV SprayDry nozzles have generated outstanding results:
- Bearding and clogging issues have been eliminated, ensuring a safer work environment and dramatically reducing maintenance frequency
- Bulk density has increased, further improving worker safety with packages that are more stable on pallets
- Scorched product caused by bearding has been eliminated, reducing waste by 1,500 metric tons per year
- Dryer temperatures have been reduced from 420°F to 380°F (216°C to 193°C), significantly decreasing overall energy consumption
- The SV nozzles consistently produce the desired drop sizes at higher pressures, boosting production while reducing waste
- Standard production runs have been extended from 12 to 20 hours – an increase of more than 65% – and have sometimes lasted up to 30 hours
- Cleaning chemicals have been significantly reduced – saving US$12,000 annually
- Daily throughput has increased by US$11,000
These factors have increased annual revenue by more than US$2.5 million and enabled Lone Star Dairy Products to recoup the investment in new SV SprayDry nozzles after just two days of operation.
For complete details of this case study click here to see the PDF version.