Pet Snacks Manufacturer Reduces Labor Costs & Product Loss with Release Spray System
Pet Snacks Manufacturer Reduces Labor Costs & Product Loss with Release Spray System
Problem:
A pet food manufacturer produces pet snacks in the form of sticks, strips, bars, and other shapes. Snack mixtures are extruded onto racks and then placed in large ovens. After baking, workers used large scrapers to remove the treats from the baking racks. The snacks frequently stuck to the racks, resulting in breakage and product loss. This process also created a safety hazard and workers occasionally cut themselves with the scrapers.
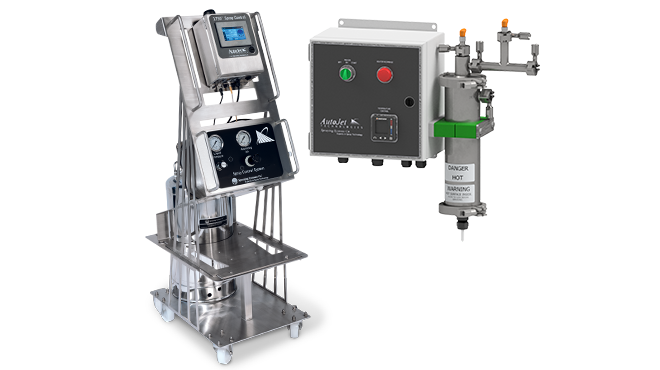
Solution:
Spraying Systems Co. installed an AccuCoat® Heated Spray System and solved the production problems by applying a food-grade release agent to their racks. Release agents viscous at room temperature, are heated to 115°F (46°C) to improve the uniformity of the spray coverage and minimize clogging problems. An AccuCoat HD15 In-Line Heater is now being used to heat the liquid on demand for optimal energy efficiency. The system is controlled by an AutoJet® 1750+ Spray Controller, which operates the in-line
heater and activates three PulsaJet® spray nozzles. All wetted spray system components are constructed of materials approved for use in food processing applications.
Results:
Adding food-grade release agents to the production process allowed the treats to easily release from the racks after baking, greatly reducing product breakage. The pet food manufacturer was able to reduce the labor used for removing treats from the baking racks by 50% and ensure a safer work environment for employees. In addition, product loss has been reduced by 20%, to less than a 2% loss. The bakery recouped the cost of the system in less than one year.
For complete details of this case study click here to see the PDF version.