Choosing the Right Tank Cleaning Equipment
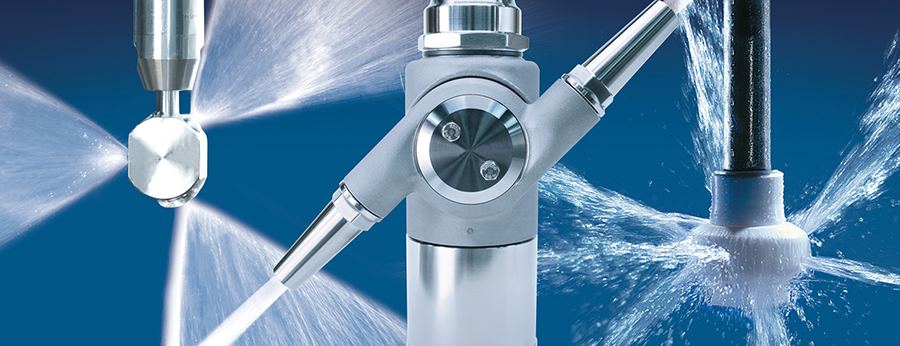
30
Apr 24
Understanding the Four Factors that Affect Cleaning Efficiency
Time, temperature, chemicals, and impact are the four key factors that influence the tank cleaning process. Understanding how each factor relates to the others is essential for selecting the optimal cleaning system in your facility. An approach which balances all four factors can lead to a more efficient and effective cleaning process while reducing costs.
Time
Time is one of the most valuable resources we have therefore efficient processes are key to profitability. A long cleaning process may ensure a spotless tank but could significantly reduce overall productivity. Conversely, a short cleaning process might not properly clean your tanks. It's essential to strike the right balance.
One such case saw a pharmaceutical manufacturer face challenges with their tank cleaning process. The traditional method, using spray balls, was not only water-intensive but also time-consuming. Seeking an efficient alternative that would reduce water usage and downtime without compromising on cleanliness, the manufacturer turned to Spraying Systems Co.'s TankJet® AA190. This innovative solution offers 360° high-impact cleaning, significantly reducing cleaning time from 1 hour to just 12 minutes. The case study underscores the effectiveness of the TankJet® AA190 in meeting the stringent cleanliness standards of the pharmaceutical industry while also achieving substantial operational savings. Read the full case study here.
Temperature
Hot water is a known solution for removing residues. However, it's important to consider the proper temperature for your application. The costs involved in heating the water or cleaning liquid can be significant and should not be overlooked.
Chemicals
With some types of residues, chemicals are needed to ensure better cleaning results. It's important to ensure your tank cleaning equipment is constructed of materials that are resistant to corrosive and acidic products.
An ethanol producer faced challenges with their previous tank cleaning methods, which were inefficient and led to extended downtime. By implementing the TankJet® 360, they experienced a significant reduction in cleaning time, water usage, and waste. The new cleaning solution not only improved the overall efficiency of their operations, but also resulted in substantial cost savings. Read the full case study here.
Impact
High impact tank and tote cleaning equipment can often improve cleaning effectiveness and result in savings by reducing the use of water and chemicals. This shortens cycles and reduces energy consumption.
IBC totes are integral for many industries to transport and store liquids. Totes are a vessel that can benefit from high impact cleaning. This case study highlights the challenge one specialty chemical manufacturer faced when cleaning IBC totes. The customer needed to clean totes with stubborn residue which had been baked on over a period of months. Our spray engineers implemented the TankJet AA190 tank cleaner, which replaced a low-pressure rotating nozzle. The TankJet AA190 operates at 500 psi (34bar) to powerfully scour all internal surfaces of the IBC totes. This helped reduce the cleaning cycle time from 45 minutes down to just 10, providing a monthly savings of $30,000.
In another instance, a manufacturer significantly benefited from switching to our automated TankJet system, which uses high-impact equipment for tank cleaning. This change not only led to remarkable water savings but also greatly improved operation efficiency. The transition streamlined their cleaning process, reducing downtime and enhancing productivity. For a deeper dive into the benefits and outcomes, explore the case study here.
Exploring the Range of Tank Cleaning Equipment at Spraying Systems Co.
We offer a wide range of tank cleaning equipment for low pressure rinsing, medium impact cleaning or high impact scrubbing of internal tank surfaces.
For those in need of high-impact cleaning solutions, the TankJet 360 or AA290 are excellent choices for large tanks, while the AA190 is tailored for medium-sized tanks. These products are especially effective for cleaning food, dairy, beverage tanks, blenders, spray drying towers, and more.
For medium-impact cleaning requirements, consider the TankJet 75 or 27500. For those prioritizing sanitary and clean-in-place (CIP) operations, the TankJet 78/78M, 80H, and 28500 are top recommendations.
In addition to these solutions, we also offer the TankJet 9 Tank Cleaning Nozzles and the TankJet 80 & 80H Tank Cleaners. The TankJet 9 Nozzles are simple, reliable, and well-suited for clean-in-place and sanitary applications, chemical distribution, and passivation. The TankJet 80 & 80H cleaners provide slow rotation for excellent dwell time on the tank surface, offering powerful, reliable cleaning. They are ideal for fermenters, food, brewery applications, and more.
If you still have questions about what tank cleaner would suit your operations best, contact one of our Spray Experts to help you find the perfect option.
Three Tank Cleaning Tips
- Heated Water vs. Impact: Hot water is costly but may be needed to remove some residues. In some cases, increasing cleaning impact may reduce or even eliminate the need for hot water. This can result in a dramatic reduction in energy use and save thousands of dollars annually.
- Reduce Cleaning Time by Increasing Impact: In some cases, a simple adjustment to liquid pressure and flow may reduce the number of cycles needed for thorough cleaning. In other cases, a different tank cleaner may be needed to generate greater impact and reduce cycle time. Faster cleaning can reduce downtime while also reducing water and chemical consumption.
- Cleaning Hard-to-Reach Areas: Internal obstructions, like agitator shafts and blades, block the spray from hitting tank walls. Having the flexibility to reposition tank cleaning equipment can make it easier to achieve complete cleaning. Utilizing equipment such as an adjustable ball fitting allows you to address the upper section of the tank and then the lower portion or alter the trajectory to target hard-to-reach spots. Additionally, specialized lances and adjustable flanges are used to precisely position nozzles. This helps ensure that the spray reaches areas with significant buildup or residue lines.
For more information on our range of tank cleaning solutions, visit our Tank Cleaning page. Our experts can help you understand and optimize the characteristics of your tank cleaning operation and help you meet your goals. Contact us today!