A Glimpse into SprayDry® Nozzles
This blog post provides an in-depth look at SprayDry® Nozzles and their role in the spray drying process, a method used to convert liquids into dry powders. It outlines the steps of spray drying, the different options we have, and what their impact is. Read on to learn more about how spray drying can help your company.
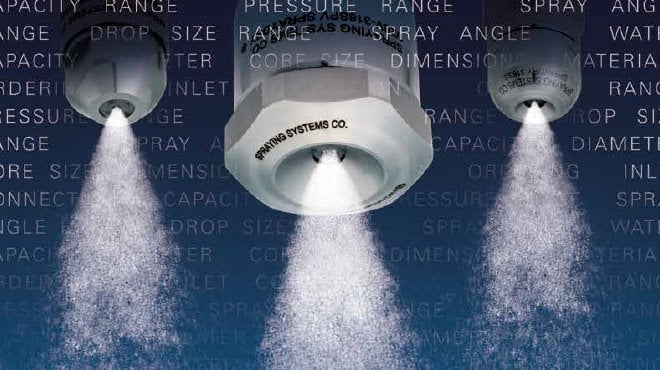
14
Nov 23
Spray Drying Overview
Spray drying is a method used to produce a dry powder from a liquid or slurry by rapidly drying it with a hot gas. Spray drying is used in various industries, including food, pharmaceuticals, and chemicals, due to its ability to produce high-quality powders with controlled properties. Here's a brief overview of how it works:
1. Introduction of Liquid: The process begins with the preparation of the feed stock, which involves formulating the liquid solution or slurry to have the correct concentration and properties for drying.
2. Atomization: As the liquid enters the nozzle, it is forced through a small orifice. This action breaks the liquid into fine droplets. The size and distribution of these droplets can be controlled by the design of the nozzle, the pressure at which the liquid is pumped, and other factors. This is a critical step as the size and consistency of these droplets will directly affect the drying efficiency and the quality of the final product.
3. Drying Chamber: The atomized droplets are introduced into a stream of hot air, initiating the rapid evaporation of water. The temperature and velocity of the air are carefully controlled to maximize drying efficiency while preserving the quality of the product.
4. Particle Formation: As the moisture evaporates, solid particles are formed. These dry particles are then carried out of the drying chamber by the airflow.
5. Collection: The dried particles are then collected, often using a cyclone separator or a bag filter. After collection, the powder is typically cooled and then packaged according to the requirements of the application. The resulting powder can then be further processed or packaged as required.
Our SprayDry® Nozzles
Our SprayDry® nozzles are known for their high efficiency, durability, and ease of assembly. Their design ensures optimal atomization, producing uniform drying and high-quality products. In addition, they comply with FDA and EU regulations. Here's a brief overview of the SprayDry® nozzles we offer.
Nozzle Type | Capacity Range GPH (L/hr) | Pressure Range PSI (BAR) | Spray Angle Range | Drop Size Range (Dv0.5 microns) | Description | |
SV SprayDry® Nozzles | Swirlchamber and orifice insert design | 4.6 to 3,003 (17.4 to 11,366) |
200 to 10,000 (13.8 to 690) | 49° to 90° |
20 to 650 | - Largest maximum free passage - Ideal for spraying slurries with high solids such as milk and whey |
SK SprayDry Nozzles | Slotted core and orifice insert design | 2.8 to 400 (10.6 to 1514) |
500 to 7,000 (35 to 480) |
44° to 90° | 30 to 150 | - Low flow rates - Small droplets that evaporate quickly - ideal for infant formula and pharmaceuticals |
SB SprayDry Nozzles | Slotted core and orifice insert design | 38.9 to 1,508 (147 to 5,708) |
500 to 7,000 (35 to 480) |
34° to 109° | 40 to 200 | - Spray viscous liquids effectively - Ideal for flavorings and dairy products |
WhirlJet SprayDry Nozzles | Whirlchamber and orifice insert design | 10.2 to 3,019 (39 to 11,427) |
100 to 5,000 (7 to 340) |
19° to 104° | 50 to 1000 | - Coarser droplets - Lower pressures - Ideal for coffee and detergents |
For a more in-depth understanding of our SprayDry® technology and its advantages, explore this bulletin or contact our spray experts.
How Can You Enhance Your Spray Drying Operations with Us?
Our nozzles are not just machine components but the heart of the entire process. At Spraying Systems Co., we understand the significance of this, and our experts will work with you directly to ensure your operations are running to their maximum potential. Here are why our nozzles stand out among the rest:
-
• Extended Wear Life: Durability and longevity are critical factors for industrial equipment, directly impacting operational efficiency, maintenance costs, and production downtime. The durability of our nozzles is attributed to the high-quality materials and innovative designs, which increase their life cycle.
• Minimize Clogging: Nozzle clogging can significantly hinder the efficiency and quality of spray drying processes. It's a prevalent issue that can be hazardous, often leads to inconsistent product quality, and increases downtime. Understanding these challenges, we engineer our nozzles to limit clogging. • Optimize Results: Our advanced spray labs innovate daily, focusing on refining and improving to guarantee that each Spraying Systems nozzle exemplifies quality and performance. Factors like drop size, spray pattern, and coverage are crucial to optimize your spray dryers. Our Spray Analysis and Research Services team conducts tests based on your specifications to develop the ideal system for your facility. Want our SARS team to optimize your system? Click here to fill out our contact form.
The Impact Our Nozzles Have
Spray drying is a delicate process; the proper nozzle can make all the difference. In a notable case study, a prominent food ingredient manufacturer transitioned to our multi-orifice 3SK SprayDry® Nozzle. The results that the manufacturer saw were:
-
• Enhanced Safety: Bearding and clogging were eliminated, reducing risks, and ensuring a safer production environment.
-
• Boosted Efficiency: With our nozzles, they achieved uniform drop sizes, leading to a 20% increase in production and minimized waste.
-
• Impressive ROI: The switch to our nozzles improved their process and led to an astounding annual revenue increase of over US$2.5 million.
To read the full case study, click here. Additionally, if you would like to learn more about our SprayDry technology and how it can help your operations click here to speak with a Spray Expert.