5 Strategies to Minimize Nozzle Clogging
Nozzle clogging is a common yet inconvenient problem, affecting operational efficiency and product quality. Learn more about the primary causes of nozzle clogging and five actionable strategies to mitigate this issue.
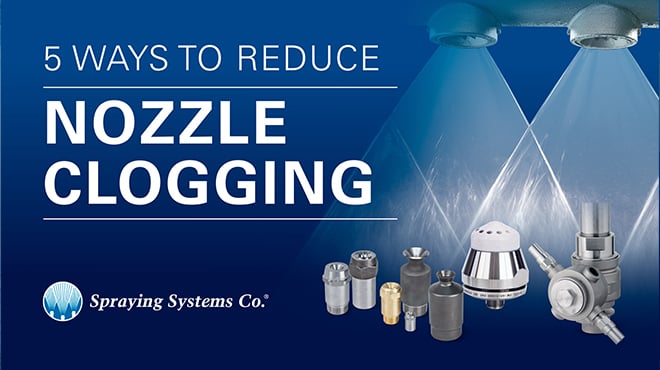
3
Nov 23
5 Strategies to Minimize Nozzle Clogging
Spray nozzles are precisely engineered components crucial in coating, cooling, and cleaning operations. They are vital to maintaining product quality for many manufacturers and processors. Underperforming nozzles can lead to costly product waste and unexpected downtime.
Nozzle clogging is an issue in many spray systems, impacting their performance and efficiency. Clogging can negatively affect spray coverage, flow rate, and droplet size. The results of your application may suffer, and in many cases, you may need to halt operations to clean or replace the nozzles. Understanding the causes of nozzle clogging is the first step toward effective prevention.
What Factors Cause Nozzle Clogging?
Nozzle clogging can be caused by two main factors: particulates in the fluid and the physical properties of the fluid, specifically its viscosity.
1. Presence of Particulates: The primary cause of nozzle clogging is the presence of particulates in the fluid which can obstruct fluid flow as they accumulate within the nozzle. These particulates stem from various sources such as raw material contamination, system corrosion, inadequate filtration, or environmental debris. The size of these particulates influences the likelihood of clogging; larger particles can quickly block a nozzle or cause wear that alters the spray pattern and performance.
2. Physical property: The type of fluid being sprayed plays a significant role in nozzle clogging. The viscosity of the fluid has a direct impact on the frequency of nozzle clogging. High-viscosity fluids tend to flow slower and can create significant buildup within the nozzle's internal passages over time. This buildup can obstruct the flow and eventually lead to clogging which disrupts the spray pattern and diminishes the efficiency of the spray system.
How To Decrease Nozzle Clogging
1. Use Large Free Passage Nozzles:
Nozzles such as Maximum Free Passage (MFP), FullJet®, or SpiralJet® nozzlesare designed with open passageways to minimize the risk of clogging. By allowing larger particles to pass through, these nozzles can maintain a consistent spray pattern and flow rate, even for challenging liquids.
By using large free passage nozzles, you can experience benefits like:
- • Minimizing the risk of clogging while using debris-filled or recirculated liquid
- • Improving product/process quality
- • Reducing unscheduled downtime
2. Install Strainers:
Strainers can be installed to filter out particles that could cause blockage. By catching these particles before they reach the nozzle orifice, strainers can significantly reduce the risk of clogging. Strainers come in two forms: integral and T-style. Integral strainers (pictured) are ordered as part of the nozzle itself. T-style strainers are designed to minimize pressure drops and provide easy cleaning and maintenance.
3. Heat Viscous Fluids:
The process of heating viscous fluids can significantly reduce their thickness and minimize the risk of blockages. This technique is valuable in scenarios where highly viscous fluids are being used. For instance, by incorporating a heated spray system or spray manifold, your company can now handle previously un-sprayable substances like peanut butter or chocolate. One notable customer that implemented our AccuCoat® Pan Spraying System, achieved an impressive 78% increase in production.
4. Use Self-Cleaning Nozzles:
Incorporating self-cleaning nozzles into your spray system can be a game-changer, especially if nozzle clogging has been a recurring issue. Self-cleaning nozzles are designed with mechanisms that automatically clear blockages, reducing the need for manual cleaning and minimizing downtime. These nozzles can be beneficial in applications where blockage is a frequent issue.
By understanding the root causes of nozzle blockage and integrating effective preventative measures like self-cleaning nozzles, a company can ensure the longevity and efficiency of their spray systems. Implementing self-cleaning nozzles into your systems can result in:
- • Reduced downtime
- • Optimal performance
- • Cost-efficiency
Click here to read more about a company that saw annual savings of $25,000 by recycling 500,000 gallons of wastewater.
5. Implement a Brush-Type Header:
Brush-type headers are designed to maintain the efficiency of nozzles mounted on spray headers commonly used to cover the width of conveyors. Over time, the nozzles can become clogged leading to a reduction in performance.
Brush-type headers include an internal brush mechanism, which can be rotated periodically to remove any accumulated debris from the nozzle. Once the cleaning is done, a valve is opened to flush the debris from the header, ensuring the nozzle remains unobstructed and functioning optimally.
There are two main types of Brush-Type headers:
- • Manual Headers: This type of header requires a maintenance worker to rotate a handwheel to initiate the cleaning process. It is a hands-on approach that offers simplicity and direct control.
- • Automatic Brush Header: For those seeking a more streamlined approach, the automatic version comes equipped with a motor and timer. This means that at predetermined intervals, the cleaning process is automatically initiated, eliminating the need for manual intervention.
Benefits of Brush-Type headers include:
- • Hassle-free operation and installation.
- • Minimized operator intervention, especially with the automatic version.
- • Negligible maintenance requirements, ensuring long-term efficiency.
For a visual demonstration of how the automatic brush header works, watch this video. Whether you opt for the manual or automatic version, brush-type headers promise to enhance the longevity and efficiency of your system.
Regular Nozzle Maintenance is Key
Even with these preventative measures, regular nozzle maintenance is essential to ensure optimal performance. This includes regular inspection and cleaning of the nozzles, even if the spray appears to be functioning well. The recommended maintenance intervals can vary based on the type of nozzle and the fluid being sprayed. Click here to watch our recommendations on nozzle maintenance.
If you are experiencing issues with nozzle clogging in your spray application, contact our spray experts for advice tailored to your specific situation.
Remember, the key to minimizing nozzle blockage is understanding the causes and implementing effective preventative measures. By choosing the right nozzles and equipment for your application, you can maintain optimal performance and minimize downtime.