British Automotive Forging Company Quadruples Productivity in Relation to Lubricant Consumption
British Automotive Forging Company Quadruples Productivity in Relation to Lubricant Consumption
Problem:
Stokes Forgings, the largest automotive forging company in the UK, needs properly lubricated wheel hub molds. Stokes was using compressed air to propel the lubricant via pipe into the die. The costly, graphite-based lubricant was consistently over applied. The over-application was a profit drain, resulted in manual rework of some wheel hubs and created a messy, unsafe work environment in and around the press.
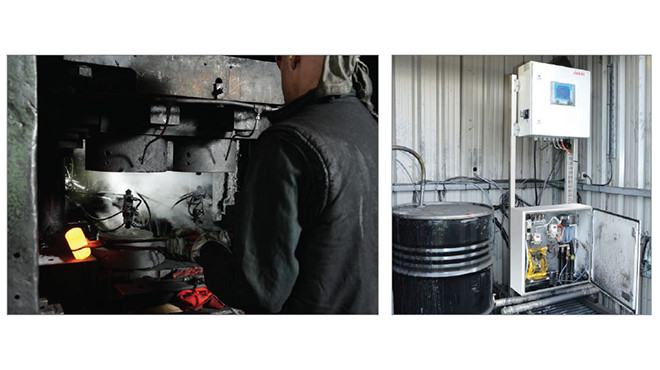
Solution:
The Spraying Systems Co. solution was an AutoJet® Lubrication System. The automated system delivers precise amounts of oil to lubricate the mold.
The system is controlled by an AutoJet spray control panel with a touch screen controller which enables accurate adjustments to the flow rate and spray timing to be made easily. The movements and operation of the system are synchronized with those of the press.
Four D55500 air atomizing nozzles equipped with automatic clean-out needles dispense the oil. The nozzles are supplied by a diaphragm pump mounted in a mobile base unit. All nozzles are contained in the coil lubricator unit which includes an oil mist extractor to prevent misting and worker inhalation problems. Automatic solenoid valves ensure excess oil is returned to the correct supply tank. The oil is filtered on the suction lines to ensure no contaminants enter the system.
Results:
The AutoJet® Lubrication System from Spraying Systems Co. has eliminated overspray, saving money by significantly reducing the amount of graphite lubricant wasted. The elimination of overspray has also resulted in a cleaner, safer working environment. The new system uses lubricant so efficiently that Stokes is now able to forge four times as much product using the same amount of lubricant. The new system has also improved quality, virtually eliminating the need for manual rework.
Stokes is saving £2000 (over US$3,000) each month, on the graphite lubricant and has experienced a nine-month payback on the system. The company is so pleased with the results that they plan to convert all their presses to the new system.
For complete details of this case study click here to see the PDF version.