Snack Food Producer Reduces Water Use
Snack Food Producer Reduces Water Use
Producer reduces water use by 500 million gallons and saves $10 million by making one small change
Problem:
CONTRIBUTE TO MULTI-YEAR SUSTAINABILITY GOAL OF REDUCING WATER USE BY 25% BY 2025
Food processing is one of the most water-intensive industries. Water is used as an ingredient, during processing and for cleaning and sanitation. One leading snack food producer with a strong commitment to sustainability turned to Spraying Systems Co. to help uncover saving opportunities.
During an initial water audit at one plant, we determined the nozzles being used to clean corn chip lines were oversized for the operation. The nozzles were very effective, but the flow output was more than what was required for cleaning. We were confident the same style nozzle operating at lower flow rates could achieve the same level of cleaning and dramatically reduce water use. Testing by the producer verified there was no difference in the cleaning effectiveness of the two nozzles and the lower-capacity nozzle reduced water use by 80%.
While the reduction in water use resulting from changing nozzles was impressive, it seemed like a very small change in a very large operation. The snack food producer was concerned that changing nozzles wouldn’t have a big impact on its sustainability initiative. So, we ran some calculations to estimate the potential savings if the change was made in all the producer’s plants in North America. The total decrease in water use was substantial – more than 500 million gallons.
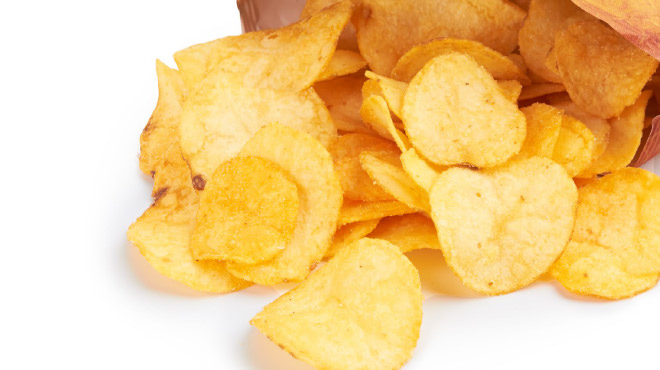
Solution:
We dispatched our local spray experts to more than 30 plants to identify and document the location, flow rate and operating pressure of all the nozzles being used to clean chip lines. Each plant was using more than 400 nozzles, operating at 350 psi and spraying just over 7 gpm. Each nozzle was in use 5,200 hours per year. By making the change to the lower capacity nozzles, each plant reduced water use from 6.4 million gallons to just 1.2 million gallons per year.
Results:
By replacing 10,000 nozzles, the snack food producer:
- Reduced water use by 500 million gallons per year
- Saved more than $ 3 million on water and wastewater treatment
- Saved $7 million by heating less water prior to cleaning
The investment in the new nozzles was recouped in less than five days, providing the snack food producer with a substantial economic benefit in addition to operating more substantially.
Replacing nozzles on the chip line turned out to be just the starting point. During plant visits, our teams identified similar water-saving opportunities during cleaning of other lines and mixing tanks. The next phase of changes is expected to save the snack food producer an additional 500 million gallons annually.
For complete details of this case study click here to see the PDF version.