Case Study
Gold Producer Saves over US$30,000 Annually with New Manual Brush-Type Headers
Over two hundred hours of maintenance eliminated per year.
Problem:
Goldcorp, a leading international gold producer, used two headers on each of three conveyors with vibrating screens to spray water on gold ore after crushing. The headers were pipes drilled with 1/4" holes fit with plastic deflectors. The holes clogged frequently, required frequent cleaning and didn’t consistently filter the gold ore.
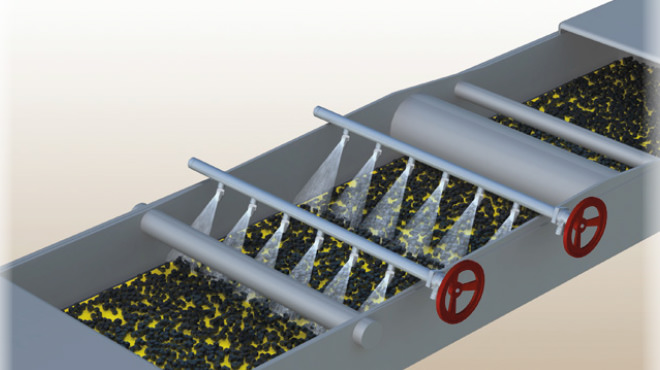
Solution:
Goldcorp now uses six manual brush-type headers to spray the water on the crushed ore. Each header is equipped with six FlatJet® nozzles with disc strainers and an internal brush. The strainers prevent clogging and allow water to continue to flow, even when debris is present. To remove the debris, the brush is manually rotated using a hand wheel. The debris is flushed away without disrupting shower operation.
Results:
For Goldcorp, the use of the manual brush-type headers improves the consistency and effectiveness of the filtering process and prevents clogging. The headers eliminate more than 205 hours of maintenance per year and reduce energy consumption due to better operating efficiency. Goldcorp saves over US$30,000 annually and the cost of the headers was recouped in just seven months.
For complete details of this case study click here to see the PDF version.