Steel Mill Improves Quality and Reduces Oil Costs by 89%
Steel Mill Improves Quality and Reduces Oil Costs by 89%
Problem:
A steel mill in Brazil was using a homemade system to spray protective oil on carbon steel used for fabrication of white goods. The oil prevents oxidation during transportation from the mill to the appliance manufacturer. The spray system, a positive displacement pump and hollow cone nozzles, did not consistently apply a uniform coating of oil, so coverage was uneven. Quality issues were severe and the mill was in danger of losing an important customer. The system also wasted oil, creating a messy work environment and a danger to workers.
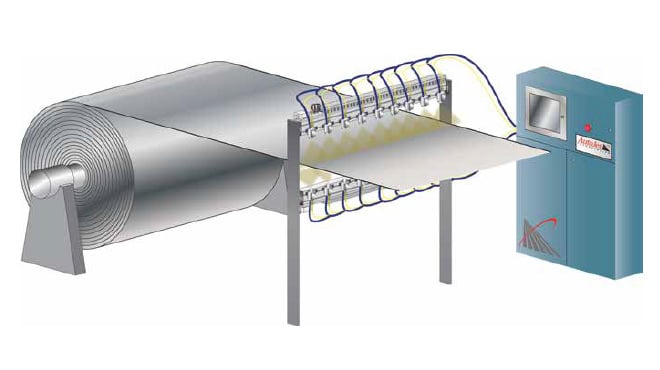
Solution:
The Spraying Systems Co. solution was an AutoJet® Lubrication system featuring a PLC spray controller and two spray headers. The headers, positioned above and below the strip, are each equipped with nine PulsaJet® automatic spray nozzles with air atomizing spray set-ups. The system uses sensors to monitor line speed and Precision Spray Control (PSC) automatically adjusts the flow rate. A consistent application rate of 600 mg/m2 (0.002 oz./ft.2 ) of oil is applied despite line speed variations ranging from 650 to 1000 m/min. (2130 to 3280 ft./min.).
The system also uses zone control to accommodate strip widths ranging from 700 to 1100 mm (27.5 to 43 in.). Nozzles are turned off when narrower strips are run.
Results:
The new AutoJet® Lubrication system solved the mill’s quality problems and prevented the loss of a key customer. By consistently applying the precise volume of lubricant required, oil costs have decreased by 89%. The cost of the system was recouped in less than five months. In addition, through precision application, overspray has been reduced and worker safety improved.
For complete details of this case study click here to see the PDF version.