Pork Processor Saves US$14,000 Annually on Compressed Air & Labor with New Blower System
Pork Processor Saves US$14,000 Annually on Compressed Air & Labor with New Blower System
Problem:
A leading Midwest pork processor needed to dry two overhead chain conveyors in its hog slaughter facility. The chains, which are wet from the overnight plant sanitation process, must be thoroughly dried each morning. If the chains are not dry, the oil-based lubricant applied to the chains prior to processing drips onto the carcasses. The contaminated areas of the carcasses must undergo labor-intensive hand trimming. The chains were previously dried using compressed air at 125 psi (8.6 bar) through ¼” open pipes. Three sanitation employees, each equipped with a ¾” open pipe, supplemented the drying provided by the stationary pipes.
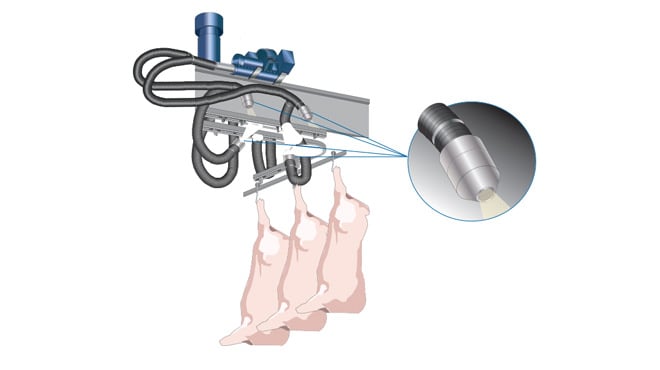
Solution:
Spraying Systems Co.’s solution was a WindJet® Air Cannon Package, which was installed above the processing floor. The system consists of a 20HP blower with eight ½” air cannons, four directed at the dress chain conveyor and four directed at the weigh chain conveyor. The WindJet system includes a low-maintenance regenerative blower that produces clean, high-impact air. The blower is extremely energy-efficient and produces very low operating noise. WindJet Air Cannons operate for 45 minutes each morning, delivering a uniform, high-velocity air stream that dries the chains more efficiently than ever before.
Results:
The processor eliminated the cost of compressed air and was able to re-assign the sanitation workers to other tasks. These factors combined to save about US$14,000 annually, resulting in a payback period of 12 months for the WindJet® Air Cannon Package.
For complete details of this case study click here to see the PDF version.