火力発電所では、ノズルを切り替えたことで年間約1500万円のコスト削減に成功
火力発電所では、ノズルを切り替えたことで年間約1500万円のコスト削減に成功
問題:
ある火力発電所では、高価なコンプレッサーエアーの使用と、スプレードライヤー吸収機のメンテナンス頻度を減らしたいと考えていました。酸などの汚染物質を排気ガスから取り除くためには石灰スラリーをSDAタワーへ注入する必要がありますが、石灰スラリーはスプレーが困難な材料です。
ノズルメンテナンスの頻度が高い点も問題となっていました。ノズルに堆積して乾いたスラリーを取り除く危険な作業を、作業員2名で、毎日最長3時間も行っていました。
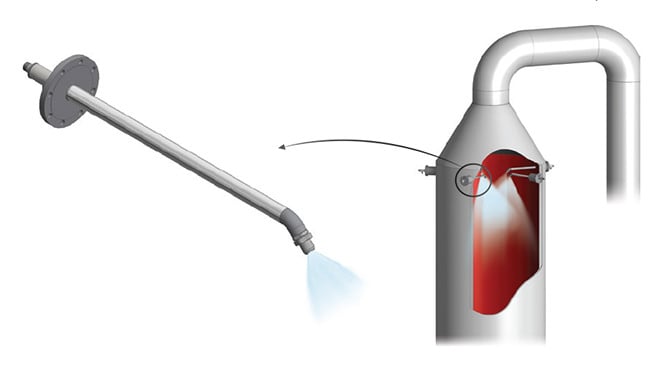
解決策:
CFD(数値流体解析)とFloMax固着防止ノズルにより、問題を解決しました。
SDAタワーのCFDモデルを制作することで、気体の流れをより具体的に把握することができます。それをもとにスプレーパフォーマンスとランスの最適化を可能にします。予測したSDA内の気流を基に設計された4個のFloMaxノズルランスは、コンプレッサーエアーの使用量を最小限に抑えながら、正確な粒子径と最適なドライ率を提供し、効率的に石灰を散布します。
またCFD解析により、ノズルランスの設置場所を的確に定めることが可能です。ノズルは45.7 mのSDA底面から、34.1 mの高さで設定し、特定の角度でスプレーする長さ1.2 mのランスが使用されました。FloMax固着防止エアーキャップにより、ノズルへの蓄積は軽減され、毎日のノズルメンテナンスが不要になりました。
結果:
FloMax ノズルランスへ変えたことにより、石灰スラリーを注入する際に使用し
ていたコンプレッサーエアーの消費量が減少しました。そのため、以前のシステ
ムで使用していた200HP コンプレッサーが不要になり、年間約980 万円の費用が
削減されました。また、毎日のノズルメンテナンス費用年間約613 万円も加味す
ると、年間約1500 万円のコスト削減に成功しました。
さらに、メンテナンス作業員の安全にかかわる問題が解消されました。サステ
ナビリティの観点から見ると、排気コンプライアンス率は大きく改善し、200HP
コンプレッサーを使用しなくなったことにより、エネルギー使用も著しく減少し
ました。