OPTIMAL DRYING OF PACKAGING FILM WITHOUT THE USE OF COMPRESSED AIR
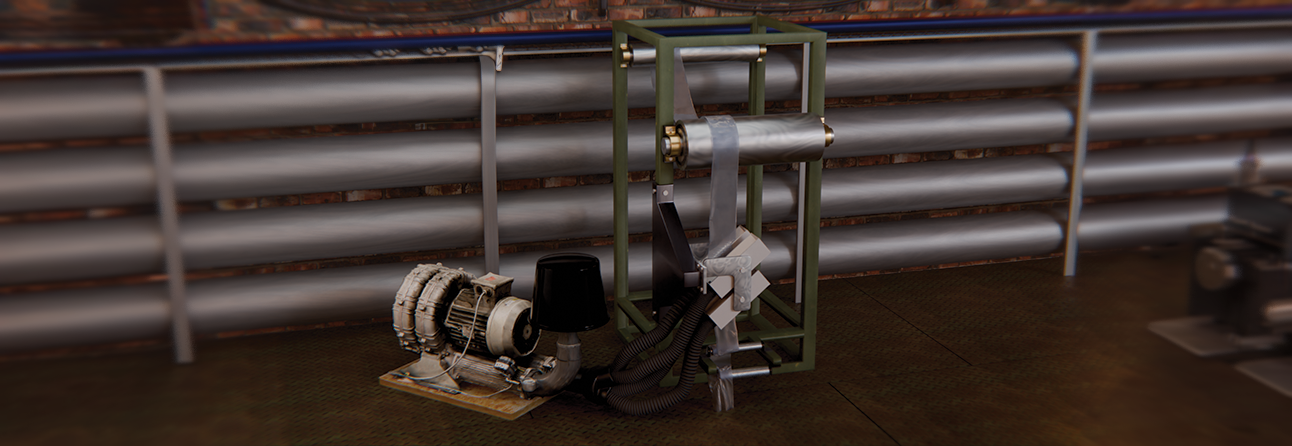
18
Mar 24
Recently we were contacted by a company that specializes in the production of plastic packaging films - primarily used for food products. The film is produced at very high speed (up to 150 m/s) with a width variation of 50 to 200 mm. To make up for the variations they use 5 separate production lines. The product is extracted at a temperature of 200°C before being cooled off in a bath. After this process the film is dryed. Depending on the quality of the raw material it takes up to 3 different drying stages to receive the expected result. At the end of the process the finished product is rolled on a reel for shipping,
The drying process is essential to ensure the product meets the customers’ expectations. Unfortunately the producers have been struggling with this part of the production process. Even after trying different approaches they couldn’t find a performant solution that could fully dry the film. An underdimensioned turbine provided too little flow rate and even a drying cloth at the end of the drying process wasn’t enough to dry the film.
Customers started complaining about the product quality. The film producer needed a more performant drying solution, so they set the following goals:
- No more water residue on the packaging film
- No more expensive compressed air consumption
- Capable of drying at varying widths and high speeds
Solution
With over 80 years of experience in spray technology and a large selection of dedicated drying products we were the ideal partner for this project.
To determine the necessary solution we first assessed the situation at the packaging film production facility. Based on these visits we proposed a new system that would utilize a new air blower with 4 air knives placed in at an optimal angle.
Once we agreed on the new approach we set up a test environment on one of the production lines for validation. As soon as the customer was happy with the results we were able to start rolling out the new solution.
The new drying solution was installed on 5 lines and consisted of:
- 3x Air blower systems per line
- 4x Air knives per blower system
Results
The producer of the plastic packaging films was happy to note that their expectations were met. They are finally able to properly dry the films to meet their customers’ quality requirements. More importantly, they are able to do this without using compressed air. This has a big impact on the production process costs.
Furthermore, the new drying approach means that all 5 production lines are now using the same equipment. This standardization makes it easier to maintain everything and optimize performance.