Switch to Regenerative Blower Saves Tube Manufacturer US$100,000 Annually
Switch to Regenerative Blower Saves Tube Manufacturer US$100,000 Annually
Problem:
A manufacturer of cut-to-length steel tube and pipe needed a more reliable way to ensure its finished product was free of metal chips and residual cutting fluids before shipping. An existing compressed air blow-off system was costly to operate and ineffective. As a result, extra labor was required to inspect the material after it was stacked and to manually blow out chips.
Customers still rejected several shipments each month. Extra transportation and labor costs were incurred for the material to be returned to the shop, thoroughly cleaned and reshipped.
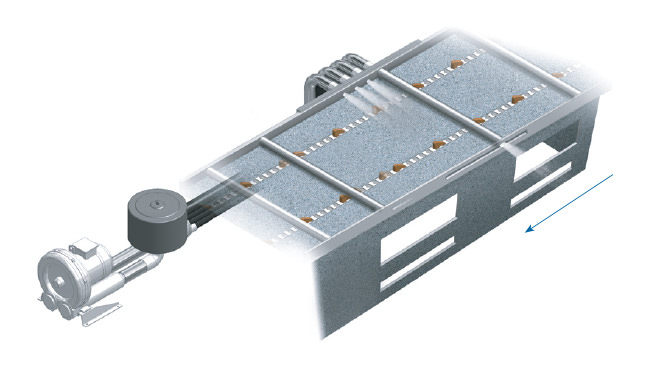
Solution:
A WindJet® Air Cannon Package using four air cannons and a 20 HP regenerative blower solved the customer’s problem. The air cannons are mounted side by side and blow continuously across an adjustable-width track conveyor that moves the cut tubing to a stacking and bundling area. The tubes are blasted by high velocity, low pressure air as they pass by, removing all metal chips and cutting fluid from tubing up to 10 feet long.
Besides being more energy efficient than a compressed air system, the regenerative blower’s variable frequency drive enables blower speed to be turned down when shorter pieces are being produced for additional energy savings.
Results:
Installing the WindJet® Air Cannon Package eliminated the use of compressed air for blow-off, immediately reducing power consumption for this activity by about a third. It also cut post-processing labor requirements in half, enabling the company to reassign staff to other tasks. Significant additional savings have come from eliminating the transportation costs for rejected shipments.
Together these factors provided a payback period of slightly less than nine months. Cutting electricity use and eliminating reject-related trucking have also reduced the operation’s carbon footprint significantly, increasing sustainability.
Just months after installing the WindJet Air Cannon Package on one production line, the manufacturer ordered another system for its second production line.
For complete details of this case study click here to see the PDF version.