Specialty Powder Manufacturer Saves Over US$75,000 Annually on Tank Cleaning Labor
Specialty Powder Manufacturer Saves Over US$75,000 Annually on Tank Cleaning Labor
Problem:
A leading producer of powders used for precision polishing in the electronics industry needed to thoroughly clean the interior surfaces of its processing vessels. Manually cleaning the powder residue from 12’ x 20’ (3.7 m x 6.1 m) ribbon blenders with high pressure hoses took up to twelve hours. Obstructions within the blender made it a slow process and there were also concerns about worker safety. The cleaning process represented a significant labor expense and the loss of production time severely limited manufacturing flexibility.
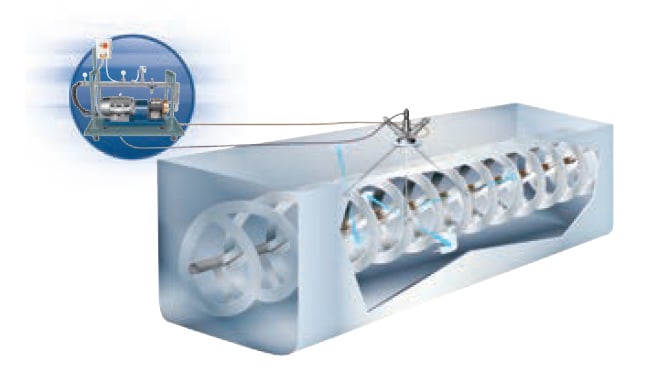
Solution:
Spraying Systems Co.’s TankJet® AA190AGH and AutoJet® Fluid Delivery System provides automated, effective cleaning of the entire blender interior. Hot water is pumped to the TankJet tank cleaner by the fluid delivery system at 1000 psi (70 bar) with a flow rate of 20 gpm (75 l/min).
The six foot shaft of the TankJet unit, equipped with a Model 43047 adjustable ball fitting, allows flexible positioning of the spray turret in the blender. To avoid a shadowing effect caused by the ribbon blade that runs horizontally through the blender, the spray turret is repositioned twice during the cleaning cycle to ensure complete coverage. Operating at high pressure provides powerful impact and has decreased the cleaning time to about 45 minutes and workers no longer need to enter the blender.
Results:
After successfully testing the automated system on a single ribbon blender, the customer equipped a total of seven vessels with TankJet® cleaning equipment. The AutoJet® Fluid Delivery System is mounted on a base with lockable casters for easy movement in the production facility. Automating the cleaning process with the TankJet tank cleaner and the AutoJet Fluid Delivery System has cut the cleaning time for the ribbon blenders by more than 90% for an increase in production time and greater manufacturing flexibility. The labor savings amounts to more than US$75,000 annually. The equipment cost was recouped in approximately 9 months.
For complete details of this case study click here to see the PDF version.