New Spray Nozzles Increase Beef Processor’s Daily Revenue by US$29,000
New Spray Nozzles Increase Beef Processor’s Daily Revenue by US$29,000
A major international beef processor needed to chill steer carcasses in a more efficient manner. A combination of full cone and wide-angle flat spray nozzles are now used to provide complete, mist-free water coverage on the carcasses for effective cooling.
Problem:
A major international beef processor needed to chill steer carcasses in a more efficient manner. The process, which involved spraying the carcasses with over 50,000 gallons (189,271 liters) of chilled water over an 18-20 hour period, is used to prevent weight loss and shrinkage.
The previous system was not providing complete coverage of the carcasses and required long chilling times. As a result, carcass mass and size were reduced causing unnecessary revenue loss. In addition, excess mist was generated by the spray system creating ice build-up on the rails and the facility structure. The nozzles required frequent maintenance and constant monitoring in order to keep the chill rooms operational and safe.
The beef processor sought a better spray system to increase chill room efficiency, ensure complete carcass coverage and lower maintenance needs.
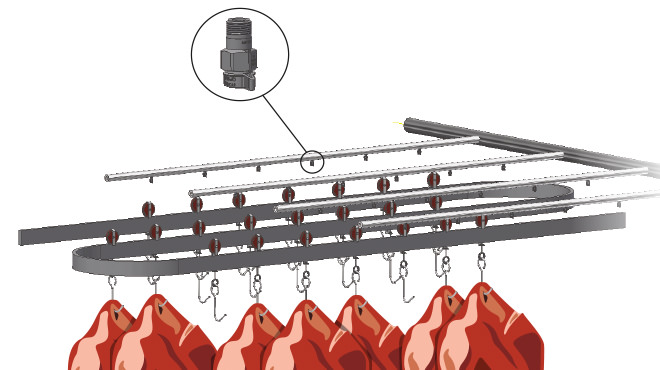
Solution:
Spraying Systems Co. converted one of the processor’s 11 chill rooms to ProMax® QuickJet® nozzles. A combination of full cone and wide-angle flat spray nozzles are now used to provide complete, mist-free water coverage on the carcasses for effective cooling. A third-party review validated that chill time had decreased, and water consumption and ice build-up on the rails and refrigeration equipment was significantly reduced. It was also verified that carcass weight loss was minimal during the cooling process.
Results:
With cooling time cut in half, a significant drop in water usage and a product yield increase due to a reduction in carcass shrinkage, the remaining 10 chill rooms were also converted to the ProMax® QuickJet® nozzles. The company now processes an average of 1750 steer a day with each carcass weighing approximately 450 lbs (204 kg). The 2% increase in production yield and 44% decrease in water consumption have resulted in a daily revenue upturn of nearly US$30,000. In addition, the new system enhances the processor’s sustainability efforts by saving a total of 4.3 million gallons (16.2 million liters) per year. The estimated payback period for the conversion to ProMax QuickJet nozzles is less than three weeks.
For complete details of this case study click here to see the PDF version.