Why spray nozzles are essential for a performant cooling process
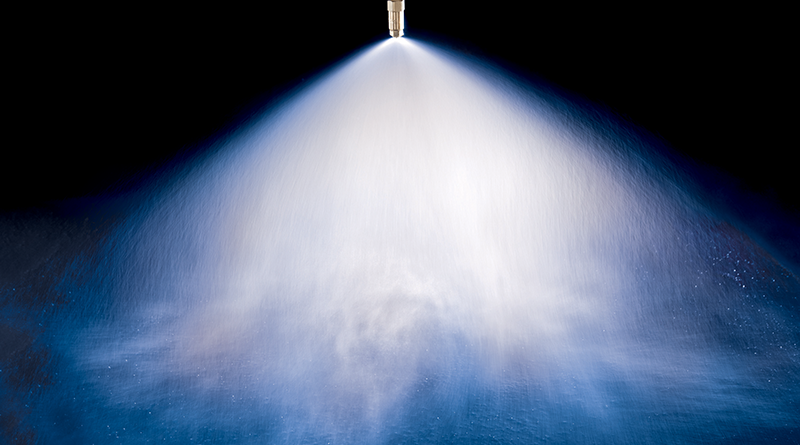
16
Oca 23
Sprays are used to cool numerous industrial processes from stamping presses to freshly forged steel and from gas turbine inlets to power plant exhaust streams. But what is it about sprays that make them an attractive cooling solution? It comes down to momentum, surface area, and vaporization.
Importance of vaporization
Vaporizing liquids takes a lot of energy. For water, it takes about five times more energy to vaporize water (transition from liquid to gas) than it would take to heat it from just-melted ice (at 0 °C) to just-about-to-boil liquid (at 100 °C). Of course, even if a liquid doesn’t vaporize it can still cool a surface. Spraying lubricating oil on a stamping press is going to cool it. But we can cool things far more effectively if we allow the liquid to vaporize. So why do sprays help with vaporization? By making the spray, we’ve created a lot more surface area between the liquid and the medium we’re trying to cool.
Surface area & heat transfer (cooling)
Why not just flood surfaces with water to cool them? There’s a limit to how much heat transfer (cooling) one can achieve with just a pool of boiling liquid. As water boils (vaporizes) it expands into a gas. If there’s enough of this expansion at the hot surface, we reach a point where the liquid never touches the surface directly. We now have a layer of gas insulating the hot surface. Spray droplets fly through the air with some momentum. Even if there’s a gas layer insulating the surface, momentum can carry droplets through.
Cooling hot gas flow
Of course, sprays aren’t only used to cool surfaces. They can be used to cool gas flows as well. In many industrial applications such as power plant exhausts, a hot gas flow must be cooled before it can enter other equipment or is released into the atmosphere. Sprays are a great choice for these sorts of applications. Because sprays have their own velocity, you can have just a few at strategic locations that still fill the duct with droplets – cooling all the gas. Strategic positioning of sprays in gas flows is key to preventing liquid droplets from hitting hot equipment causing fast evaporation. Droplet surface area in a gas flow is key to effective gas cooling.
Finally, one doesn’t have to go above the boiling point of water to benefit from spray cooling. Outdoor misters rely on vaporization to cool desert air while staying well below boiling. This principle is used to increase the power output of power generation gas turbines. Cooler air is denser. Therefore, there’s more oxygen that can enter the inlet and hence more fuel can be burned.
Spray cooling technology
Cooling plays a critical role in a wide range of applications across many industries. Spray technology is used and many of our nozzles provide the necessary spray cooling.
- • WhirlJet® hollow cone spray nozzles – evaporative cooling in spray ponds and cooling towers, gas scrubbing, washing and cooling, water aerating and water cooling.
- • VeeJet® flat spray nozzles – cooling and quenching, fire suppression/prevention, gas washing, washing/rinsing and water cooling.
- • FullJet® Full Cone and CasterJet® nozzles – heat transfer cooling in steel mill operations.
- • FloMax® Air Atomizing and HP FogJet® nozzles – gas cooling and conditioning operations.
- • Lances and Precision Spray Injectors – gas cooling.
Lab optimization solutions
To achieve optimal cooling efficiency of solids or gases, our expertise in our state-of-the-art labs provide solutions in heat transfer, drop size analysis, and process modeling to simulate our customers operating environment.
We encourage you to direct your customers to our spray analysis team to have us assist with any specialized cooling applications challenges/needs.
Cooling applications – sustainable solutions
Cooling solids
Solid objects are typically cooled using spray nozzles and headers, especially in food processing and metalworking. Examples include cooling jam and jelly jars after steam sterilization, cooling and curing concrete blocks, and poultry grow-out house cooling. Here are a couple of examples of products that require cooling to optimize coverage and minimize waste.
- • Case Study 1 Solution: Cast Iron Pipe Manufacturer Eliminates Rework and Saves US$40,000 per Month with New Spray System
- • Product Feature: HHX FullJet® Full Cone Nozzles provide consistent spray distribution to ensure uniform cooling and high heat transfer in the steel industry. They are ideal for secondary cooling operations such as billets, blooms, rounds and slabs.
- • Case Study 2 Solution: New Spray Nozzles save 2.7 Million Gallons of Water for Beef Processor.
- • Product Feature: Quick FloodJet® Flat Spray Nozzles form a flat spray pattern that is evenly distributed from the center of the spray. The deflector surface enables wider spray angles compared to other flat spray nozzles.
Gas cooling
Gas cooling can be complicated and challenging due to high temperatures and extreme environments. It’s high imperative to determine the exact drop size required to achieve the desired cooling effect without wetting. The process stream and operating conditions have a big impact on spray performance, so Computational Fluid Dynamics (CFD) is often used to identify the best spray nozzle type, drop size, placement in the gas stream and spray direction.
Gas cooling is widely used in refineries, power plants and chemical processing. Typical applications include in-duct cooling, pollution abatement, emergency quench and more.
- • Case study 1 solution: Ethylene Plant doubles production and increases profitability with new Gas Cooling Injectors.
- • Product feature: Precision spray injectors consist of a pipe with one or more customizable spray nozzles that can be tailored to deliver a specific volume of fluid at a specified pressure drop. The use of spray nozzles on the injector enables precise control over the distribution of the injected liquid into the receiving process fluid.
- • Case study 2 solution: Switching Nozzles waste-to-energy plant US$100,000 per Year.
- • Product feature: FloMax® Air Atomizing Nozzles produce very small drops with exceptional efficiency. The nozzles offer significantly higher turndown ratios than standard two-fluid nozzles for maximum operating flexibility.
There are many other spray cooling applications we test and give solutions to our customers who run into challenges:
- • Cooling steel in continuous casters
- • Quenching metals after heat treating
- • Roll cooling in steel mills
- • Cooling food jars after processing
- • Zoned cooling of roofing materials
- • Evaporative cooling for livestock and poultry
- • Cooling extruded PVC pipe
- • Spray Ponds to cool water from heat exchanger
If you'd like to learn more about our cooling applications or want to discuss a specific application please contact your local spray expert.