Plastic Cup Manufacturer Saves US$18,000 Annually with Automated Anti-Static Spray System
Plastic Cup Manufacturer Saves US$18,000 Annually with Automated Anti-Static Spray System
Problem:
A leading manufacturer of single-use thermoformed cups needed to apply a thin coating of silicone emulsion into the plastic cups after they were molded. The coating prevents the cups from sticking together during packaging and helps control dust in the manufacturing environment.
The initial method for applying the silicone emulsion was to dip the plastic sheet in a release agent before molding. This process coated both sides of the sheet when coverage was only needed on one.
Later, a PLC based spray system was used without success. The system’s slow response time and delayed spray shut-off resulted in over-application of the release agent, which inhibited downstream printing and wasted the expensive release agent. In addition, low quality spray nozzles required frequent maintenance and provided poor transfer efficiency. Misting and excessive dripping from the spray nozzles also created slippery floors in the production area.
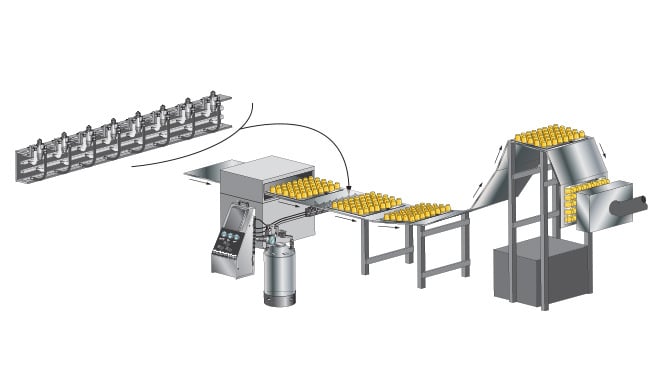
Solution:
The Spraying Systems Co. solution uses an AutoJet® Model 1550 Modular Spray System with a 16-gallon (61-liter) pressure tank to deliver the silicone emulsion to automatic nozzles spraying upward into the molded cups. The nozzles are mounted in a convenient one-piece channel header positioned below the production line immediately after the molding machine.
JAU air atomizing nozzles, with drip-free shut-off, evenly coat the interior surfaces of the cups. The automated system is integrated with the machine press to spray individual cups as they pass through the spray station.
Results:
The AutoJet® Model 1550 Modular Spray System has improved manufacturing efficiency in multiple ways. Five hours of labor that was previously needed each month for spray nozzle maintenance have been eliminated. The new spray system has also reduced consumption of the silicone emulsion by more than 15%. These two factors save the cup manufacturer more than US$18,000 per year. The system cost was recouped in less than a year. Improved spray nozzle performance and better system control have eliminated the printing problems caused by over-application of the release agent and reduced scrap. Plus, improved transfer efficiency, accurate intermittent spraying and positive shut-off have eliminated misting and dripping improving workplace cleanliness and safety
For complete details of this case study click here to see the PDF version.