OSB Manufacturer Saves CAD$150,000 Annually with New Wax Spray Systems
OSB Manufacturer Saves CAD$150,000 Annually with New Wax Spray Systems
Problem:
A manufacturer of Oriented Strand Board (OSB) needed to spray wax on wood strands in the blending process. Slack wax is sprayed on the strands to improve the efficiency of the resin binders and to enhance the board’s resistance to moisture. To ensure product quality, the flow rate of the wax must be maintained in proportion to the weight of wood strands being processed.
A previous spray system used hydraulic flat spray nozzles. The flow rate was controlled by manually adjusting the pressure of the pump. The distribution of the wax spray throughout the length of the blender was uneven. The wax flow frequently failed to match the tonnage of the wood chips being processed and over-application of the wax was a common occurrence as well.
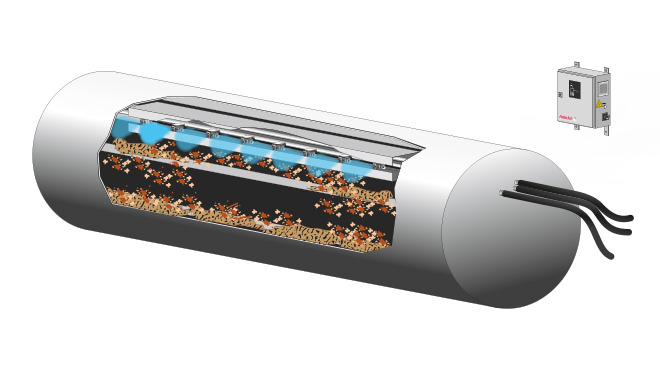
Solution:
The Spraying Systems Co. solution uses an AutoJet® Model 2008 Spray Control Panel and a header with eight PulsaJet® spray nozzles. Because the viscous slack wax must be sprayed at elevated temperatures, the header is fully jacketed and heated PulsaJet nozzles are used to ensure temperature control and proper atomization. The spray controller automatically adjusts the flow of slack wax through the electrically-actuated spray nozzles based on the tonnage of wood being processed.
Using Precision Spray Control (PSC) instead of adjusting liquid pressure to control flow rate allows instantaneous adjustment of flow and maintains optimal drop size and spray angle, ensuring uniform coverage of the wax on the wood chips.
Results:
The AutoJet® spray systems were installed in two blenders. The systems provide uniform coverage of the wood chips at a consistent application rate no matter the tonnage of chips being processed. Product quality has been maintained and slack wax consumption has been reduced by more than 5%. Total annual savings has been estimated at CAD$150,000, providing payback on the spray equipment investment in less than two months.
For complete details of this case study click here to see the PDF version.