Cereal Manufacturer Improves Worker Safety & Increases Production Time with New Cleaning Equipment
Cereal Manufacturer Improves Worker Safety & Increases Production Time with New Cleaning Equipment
Problem:
A leading producer of breakfast cereals needed to thoroughly clean the oven used for drying cereal. High pressure spray bars were used to clean the dryer belt between batches. However, the cleaning was inadequate so a worker using a high pressure spray gun was also assigned to this task. The cleaning process required more than two hours. Despite the cleaning effort, crumbs sometimes remained and caused quality problems with subsequent batches of cereal. In addition, the manual cleaning process created safety concerns because the worker had to stand on a ladder the entire time.
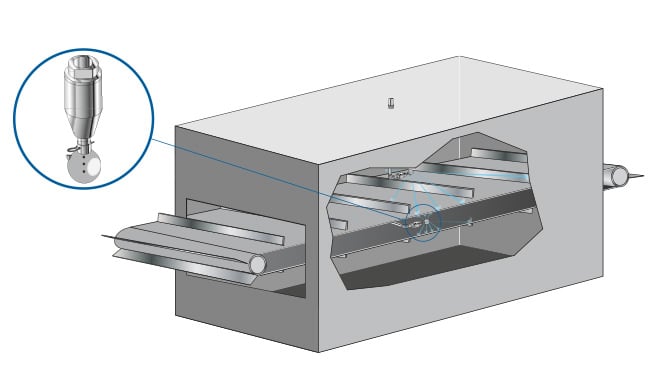
Solution:
Spraying Systems Co.’s TankJet® 14 tank cleaner solved the manufacturer’s problem. Two TankJet 14 units, one positioned above and one positioned inside the dryer belt, provide effective cleaning of the oven’s interior surfaces. Spraying at 175 psi (12 bar), the rotating action of the nozzles sweeps the cereal crumbs from the mesh belt and also cleans the dryer walls and ceiling.
Results:
The automated equipment has improved the cleaning process and eliminated the product quality and safety issues previously experienced. Workers have been assigned to other tasks. Based on labor savings alone, the TankJet® units paid for themselves in less than two months. Use of the tank cleaners has also reduced cleaning time by 15%. When the increased production time is considered, the investment in the new equipment was recouped in less than a month.
For complete detail of this case study click here to see the PDF version.