Bakery Saves More than US$70,000 Annually with New Spray System
Bakery Saves More than US$70,000 Annually with New Spray System
Problem:
A private label manufacturer of baked goods needed to apply a light coating of water and corn syrup to a sheet of dough on a moving conveyor. The solution wets the surface of the dough and acts as an adhesive for dried granular flavorings that are applied in later processing.
The manufacturer first used a spray system with hydraulic flat spray nozzles controlled by manual metering valves. Coverage was not uniform across the width of the dough sheet. Variations in line speed and breaks in the dough extrusion resulted in wasted coating since the system was controlled manually. A second system using air atomizing nozzles was also tried. It did provide a uniform coating on the dough but resulted in excessive overspray and required the installation of a maintenance-intensive mist collector.
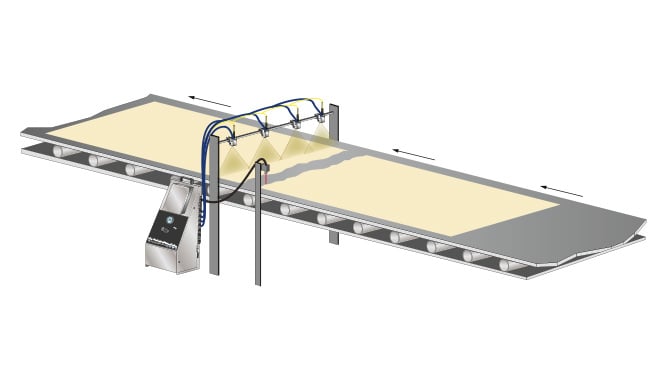
Solution:
Spraying Systems Co.’s solution uses PulsaJet® automatic spray nozzles controlled by an AutoJet® Model 1550 Modular Spray System. The easy-to-use Modular Spray System is equipped with an air-operated double diaphragm pump. The system is triggered by an external sensor that detects the presence of the dough. Precision Spray Control (PSC) is used to apply the corn syrup solution at very low flow rates providing the lightweight coverage required. Controlling the flow using PSC rather than by adjusting liquid pressure allows the nozzles to maintain optimal drop size and spray angle and ensures uniform coverage of the coating across the width of the dough. PSC also allows the system to automatically maintain the proper application rate despite changes in line speed.
Results:
The AutoJet® Modular Spray System and PulsaJet® nozzles maintain a uniform coating of water and corn syrup on the dough despite changes in line speed. Using hydraulic PulsaJet nozzles and PSC instead of air atomizing nozzles has eliminated the misting problem and need for the mist collection system. In addition, the transfer efficiency of the corn syrup solution has improved dramatically, reducing consumption of the solution by 60%. All these factors along with increased production have resulted in monthly savings of more than US$6,000 and a payback period of less than two months for the spray system.
For complete details of this case study click here to see the PDF version.