Automated Spray System Helps Cat Litter Producer Reduce Manufacturing Costs
Automated Spray System Helps Cat Litter Producer Reduce Manufacturing Costs
Problem:
A manufacturer of cat litter needed to apply precise volumes of two ingredients to the litter pellets during blending processes on a new production line. One chemical solution acts as a binder and a dust retardant. The other solution is a fragrance to improve odor control. Applying too little of these ingredients resulted in customer complaints. Applying too much was wasteful and since the ingredients are costly, it was a profit drain.
The manufacturer previously used air atomizing nozzles. Misting from the nozzles caused problems in the production area. Low transfer efficiency also resulted in customer complaints about the lack of fragrance. The manufacturer then changed to standard hydraulic nozzles. However, this required the dilution of the concentrated fragrance to achieve the proper application rates. This meant adding expensive blending equipment and an extra manufacturing step. The addition of more water to the litter also reduced the absorbing power of the pellets and the strength of pellet clumping.
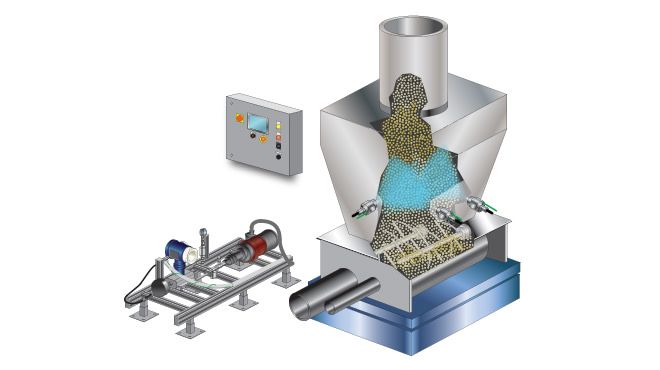
Solution:
Spraying Systems Co.’s solution consisted of an AutoJet® Spray System equipped with PulsaJet® automatic spray nozzles. These nozzles are suitable for safely spraying alcohol- and solvent-based fluids in Zone 1 rated hazardous areas. Six of the nozzles apply the binder/dust retardant solution and one nozzle applies the fragrance. The nozzles are mounted in the hoppers above the blending equipment and are fed by separate supply units for the two liquids. Each liquid supply unit includes a single-stage progressive cavity pump, a variable frequency drive unit, a flow meter and other components to ensure consistent liquid supply to the nozzles.
The PLC-based spray control panel receives a 4-20mA signal indicating the processed tonnage per hour from the production line. Precision Spray Control (PSC) is used to automatically adjust the flow of ingredients as needed. The application rates for the two ingredients are controlled independently. The ability of the system to automatically maintain the proper dosage rates as tonnage varies from startup to full production is critical for peak production efficiency.
Results:
The AutoJet® Spray System ensures consistent application rates for both the binder/dust retardant solution and the fragrance no matter the tonnage of cat litter being processed. The system has eliminated the need for the high-maintenance liquid blending equipment and the extra processing step of diluting the fragrance. Maintenance downtime has been reduced, enabling an increase in production. A payback period of less than two years is estimated for the new spray system. In addition to the financial benefits, consistent quality is ensured and customer complaints have decreased.
For complete details of this case study click here to see the PDF version.