Automated Spray System Eliminates 80,000 Pounds of Rework Each Month for Aluminum Manufacturer
Automated Spray System Eliminates 80,000 Pounds of Rework Each Month for Aluminum Manufacturer
Problem:
Jupiter Aluminum manufactures aluminum strip for use in buildings and construction. The company needed to apply a thin coating of oil on aluminum strip during the coil finishing process to facilitate forming operations and help prevent corrosion.
The previous system utilized a header with flat spray nozzles spaced over the width of the strip. All of the nozzles sprayed no matter the width of the strip and the flow rate was constant even if line speed changed. This caused several problems. Oil was wasted, especially when narrow strips were being processed. Oil was often over-applied or under-applied when line speed changed resulting in a high rejection rate for finished coils. Plus, excess oil created a messy production environment and required extra maintenance time for clean up.
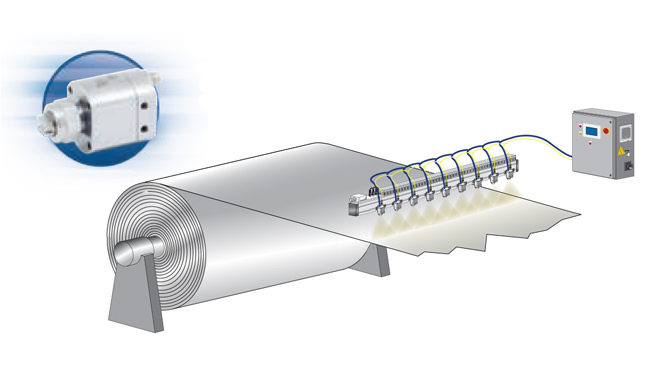
Solution:
Spraying Systems Co.’s solution uses an AutoJet® Spray System with two headers. Each header is equipped with nine PulsaJet® automatic spray nozzles. The PLC-based system allows operators to easily activate nozzles in up to four spray zones to match spray coverage to the width of the strip being processed. Operators also easily select an oil application rate on the control panel’s touch screen based on the specific product being manufactured. During operation, Precision Spray Control (PSC) automatically adjusts the flow of oil from the nozzles to accommodate line speeds which vary from 300 to 1200 ft./min. (91 to 366 m/min.).
Controlling flow rate using PSC instead of adjusting liquid pressure ensures the optimal drop size and spray angle are maintained and lubricant coverage is uniform across the width of the strip.
Results:
Since the AutoJet® Spray System was installed, Jupiter Aluminum has reduced oil consumption by more than 40%, a very important benefit for a company committed to environmental issues. Eliminating overspray has created a cleaner and safer work environment and workers are no longer needed to clean up excess oil. The greatest financial benefit is that rework on more than 80,000 pounds (36,000 kg) of coils has been eliminated now that over- and under-application of lubricant is no longer a problem. The cost of the system has been recouped in less than four months through reduced scrap, oil use and maintenance time.
For complete details of this case study click here to see the PDF version.