Tire Manufacturer Saves More Than US$20,000 per Year with New Drying System
Tire Manufacturer Saves More Than US$20,000 per Year with New Drying System
Problem:
Industrial Levorin, a tire manufacturer in Brazil, needed to dry extruded motorcycle tire inner tubes after they emerged from a cooling bath. Air knives and crimped pipes were used but these solutions were noisy, did a poor job of drying and consumed a great deal of compressed air.
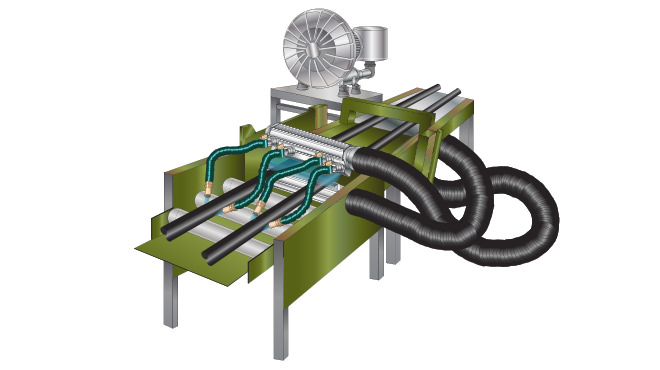
Solution:
Spraying Systems Co.’s solution consisted of two 12“ (305 mm) WindJet® Air Knives powered by a single 10 HP blower. The air knives are directly above and below the extruder line, which is right after the tubes leave the immersion bath. Additional air nozzles on flexible tubing are positioned at the edges of the inner tubes to ensure complete drying. The WindJet system uses a low-noise, low-maintenance regenerative blower which is extremely energy-efficient. The air knives deliver clean, dry, high-velocity air streams that dry the inner tubes before further processing.
Results:
The drying efficiency of the WindJet® system is far superior to the system used previously and the noise level has been reduced. Prior to installing the WindJet Air Knife package, Industrial Levorin had been spending US$31,400 annually on compressed air. The annual operating expense for the WindJet system is just over US$9,000 – an annual savings of more than US$22,000. The savings on operating costs generated a payback for the new system of just under one year.
For complete details of this case study click here to see the PDF version.