Insulated Panel Manufacturer Reduces Product Scrap, Saves US$20,000 with Automated Spray System
Insulated Panel Manufacturer Reduces Product Scrap, Saves US$20,000 with Automated Spray System
Problem:
Porter Corp, a structural insulated panel (SIP) manufacturer in the architectural design and building industry, needed to spray a mist of water onto foam boards to help activate an adhesive. Air atomizing spray nozzles were used to apply the mist, however, these would turn on as soon as the system was activated, causing overspray and erratic adhesion. This water also contaminated the adhesive, prematurely activating the curing process and forcing unplanned downtime to clean production equipment. The contaminated overspray also had to be pumped out of a collection pool into a storage container in order to be transported out of the plant.
Other issues included nozzle plugging due to water deposits, inconsistent nozzle tip alignment, excessive compressed air consumption and uneven spray coverage, which caused some of the adhesive to not activate. The spray system was unable to properly adjust the flow rate for line speed variations. Porter Corp required a spray solution that would apply water with precision at a consistently low flow rate in order to reduce scrap and operating expenses.
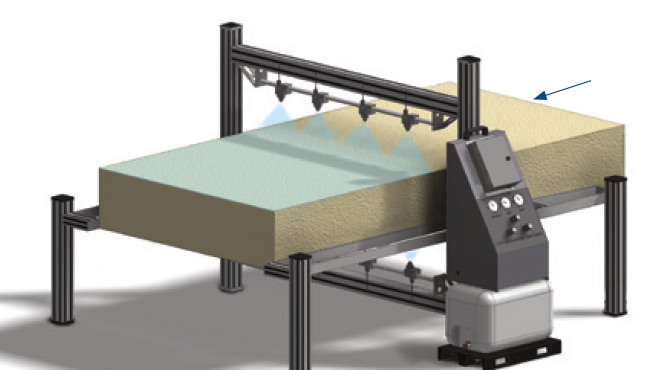
Solution:
Following a demonstration that proved the many advantages over Porter Corp’s current system, Spraying Systems Co. installed an AutoJet® Model 1550+ Modular Spray System with an air-operated, double-diaphragm pump. Eight PulsaJet® AA10000AUH electrically actuated spray nozzles and UniJet® PWMD auto-aligning, dovetail spray tips completed the system.
Triggered by an infrared photoelectric object sensor, the AutoJet system provided complete, automated spray control of the rod-mounted nozzles, ensuring uniform coverage. Providing a 50-inch (1270 mm) total spray width, the nozzles each achieved a low, adjustable flow rate of 0.45 to 1.5 gallons/hour (1.7 to 5.7 liters/hour) and virtually eliminated overspray. The system also was able to accommodate changes in line speeds, solving the many issues dealing with excess water and contaminated overspray.
Results:
Porter Corp realized many benefits from using the AutoJet® spray system, including a 50% reduction in water usage and the elimination of expensive compressed air. Consistent water coverage led to a significant boost in overall foam board quality, saving the company costs in manual labor, scrap, defect repairs, and compressed air and water consumption. All of these factors contributed to a US$20,000 annual savings and a payback period of less than a year on the new spray system.
Sustainability also was impacted due to contaminated water being reduced and plant floors being safer for workers
For complete details of this case study click here to see the PDF version.