Can Manufacturer Increases Production, Improves Quality and Reduces Scrap
Can Manufacturer Increases Production, Improves Quality and Reduces Scrap
Problem:
A can making company in the Middle East needed to wash, rinse and dry the cans to remove lubricants prior to applying a protective coating to the interior and a decorative coating to the exterior. The company was experiencing many problems with its can washer. Wash quality was poor and cans were constantly knocked over on the line and had to be scrapped
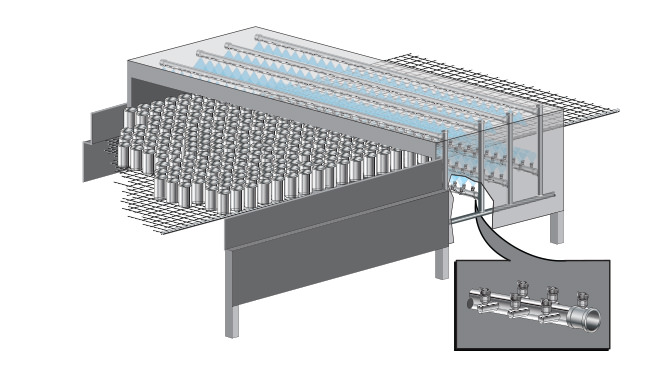
Solution:
The Spraying Systems Co. solution features special headers spraying from above and below the conveyor to ensure the cans are washed thoroughly.
The new headers are each equipped with 40 ProMax® QuickJet® spray nozzles. The quickconnect nozzles provide the same flow rates as those used previously but have a narrower spray angle, larger orifice and lower operating pressure. Larger drops are produced, improving wettability and increasing impingement on hard-to-reach areas of the cans. The nozzles also feature an internal steel washer for extra strength.
Results:
The new header system has improved the can washing process. Cans are no longer knocked over and scrap has been reduced significantly. A production increase of 13% has enabled the company to recoup its investment in the system in less than a week.
For complete details of this case study click here to see the PDF version.