Bakery Improves Quality While Reducing Material Usage & Manpower for Cake Packaging Line
Bakery Improves Quality While Reducing Material Usage & Manpower for Cake Packaging Line
Problem:
An international manufacturer and distributor of baked goods needed to ensure that cakes didn’t slip when placed on cardboard plates for manufacturing and shipping to customers. Cake movement resulted in damaged product that could not be sold and increased customer complaints.
The bakery determined that applying corn syrup to each plate as an adhesive signifi cantly reduced the number of damaged cakes. However, spraying the material proved challenging. The viscous corn syrup required heating so it could be sprayed but excessive heat caused the syrup to become stringy and unusable. Manual application of the syrup to plates required three workers. Syrup was over-applied and waste was extremely high.
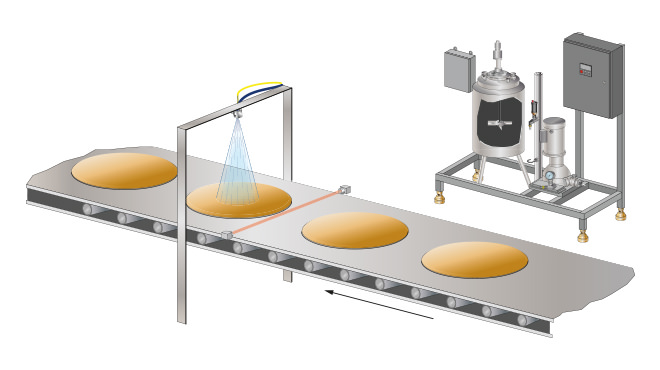
Solution:
An AccuCoat® Heated Spray System with a PulsaJet® automatic spray nozzle now applies a precise volume of corn syrup to each plate. As the cardboard plates move along the conveyor at 50 to 60 ft/min (15 to 18 m/min), an object sensor triggers the spray. The heated PulsaJet automatic nozzle equipped with an air atomizing tip applies a light coating of corn syrup to each plate in a round pattern.
The system provides precise pressure control – 30 psi (2.1 bar) air pressure and 60 psi (4.1 bar) liquid pressure – to optimize the spray performance. The system also makes automatic adjustments based on line speed to ensure accurate and precise coating of the plates.
The corn syrup fl ows from a heated 30-gallon (114-liter) pressure tank through a heated hose to the PulsaJet nozzle. An agitator in the pressure tank ensures the corn syrup is heated consistently. In addition, clean-up is easy – the control panel is NEMA 4X for wash down and a tank cleaning lance is inserted to clean the pressure tank.
Results:
Use of the corn syrup coating has significantly reduced product damaged during manufacturing and shipping and has also reduced customer complaints. The AccuCoat® Heated Spray System provides consistent coating of each cake plate and has reduced the volume applied from 7 grams to 0.5 grams per plate over manual application. In addition, the workers previously assigned to the task have been redeployed to other projects. The system cost was recouped by the plant in approximately four months through reductions in waste and labor
For complete details of this case study click here to see the PDF version.