Auto Manufacturer Reduces Oil Costs by 80%, Saves US$45,000 Annually with Automated Spray System
Auto Manufacturer Reduces Oil Costs by 80%, Saves US$45,000 Annually with Automated Spray System
Problem:
An auto manufacturer needed to lubricate the openings of fuel rails to aid the insertion of fuel pressure sensors that contained O-rings. The previous spray system, consisting of air atomizing nozzles and unregulated pumps, applied an excessive amount of motor oil, over-lubricating the parts instead of spraying them with precision. In addition, airborne misting of the oil covered nearby electrical panels and was sucked into them through cooling fans. These issues led to manual cleaning of the engine parts, equipment, production area and floors, while raising health and safety concerns for workers.
The company required a new spray solution that could address overspray, labor and safety problems.
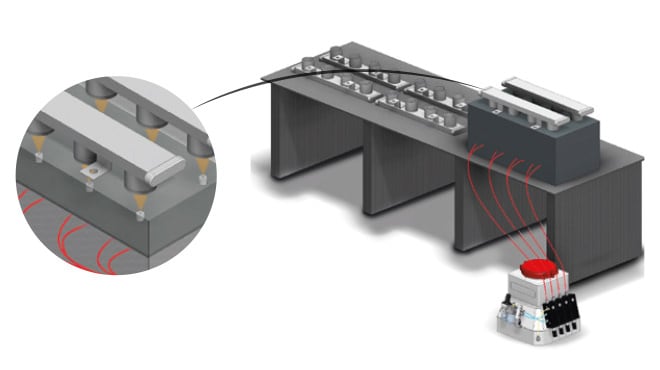
Solution:
Following a successful on-site demo, Spraying Systems Co. installed an AutoJet® L210 Lubrication System, which featured a 16-liter tank with four pumps and adjustable stroke for precise volume control. Eight Model 72100 automatic, air atomizing spray nozzles were mounted onto a fixture to lubricate two fuel rails at a time. A liquid strainer was included for filtering oil before recirculating it back into the tank.
The AutoJet L210 Lubrication System worked by drawing the motor oil from the tank through a suction filter to the spray nozzles. Each of the nozzles was supplied by air-actuated pumps to ensure uniform coverage of the fuel rail openings. These ultra-compact nozzles featured positive on-off control, which further confirmed accurate spray placement and minimized oil waste.
Results:
The AutoJet® L210 Lubrication System, in addition to four similar systems employed across various manufacturing operations, quickly paid dividends for the auto manufacturer. Oil consumption, which previously was 5 gallons (18.9 L) per day and cost US$30,000 annually, was cut to 1 gallon (3.8 L) per day, projecting to an annual cost of only US$6,000. Cleanup costs, which included manual labor over two shifts and were calculated at US$150 per day, were eliminated, adding up to a US$45,000 annual savings. When looking at the entire Spraying Systems Co. investment, the company was able to realize a payback period of only four months.
On top of its cost savings, the auto manufacturer benefitted from the sustainability impact provided by the lubrication systems. Reduced oil consumption led to less absorbent materials needed for cleanup and being sent to landfills. In turn, significantly less pollution was emitted by these materials as well as from airborne oil mist exhausted from the plant.
For complete details on this case study, click here to download the PDF version