Case Study
Radiator Manufacturer Saves with New Shower Header
Problem:
Radiadores Visconde, a Brazilian manufacturer of automotive radiators, needed to apply flux on radiator cores before the brazing furnace. The powdered flux is mixed with deionized water and then sprayed on the aluminum parts before entering the furnace. The previous system included a stainless steel spray manifold with plastic nozzles. Frequent clogging caused poor spray performance and excessive downtime to remove and clean the spray nozzles.
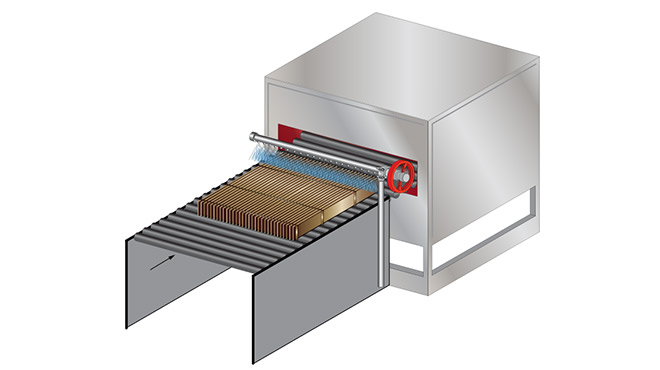
Solution:
Spraying Systems Co.’s solution consisted of a brush-type shower header spraying over the width of the conveyor. The 1000 mm (39 in.) header is equipped with 20 flat spray ShowerJet nozzles which apply a uniform coating of flux on the radiators from a spray height of 215 mm (8.5 in.). A simple turn of the hand wheel rotates an internal brush that cleans all nozzles at once. In just seconds, debris is removed from the header through a flush-out valve, restoring full liquid flow quickly and easily.
Results:
Installation of the brush-type shower header has saved Radiadores Visconde two hours of manual labor per shift and allows factory staff to be assigned to other tasks. Based only on labor costs, the payback for the new header was just under 12 months. Reduced downtime and more consistent product quality are additional benefits provided by the new spray system.
For complete details of this case study click here to see the PDF version.