Bakery Reduces Egg Wash Consumption by 50% with Automated Spray System
Bakery Reduces Egg Wash Consumption by 50% with Automated Spray System
Problem:
A bakery which supplied hamburger buns to major fast food chains needed to apply egg wash on the buns prior to baking to create a shiny appearance. The company built its own spray system, consisting of spray manifolds equipped with hydraulic nozzles. Each of the eight nozzles on each manifold was controlled by an individual solenoid valve. Two manifolds were used in order to ensure spray coverage, even if nozzle plugging occurred in one of the manifolds. However, the nozzles orifices were too small, resulting in frequent plugging and the need for constant maintenance during production. The result was a messy work environment and a 25-30% rejection rate of the buns after baking.
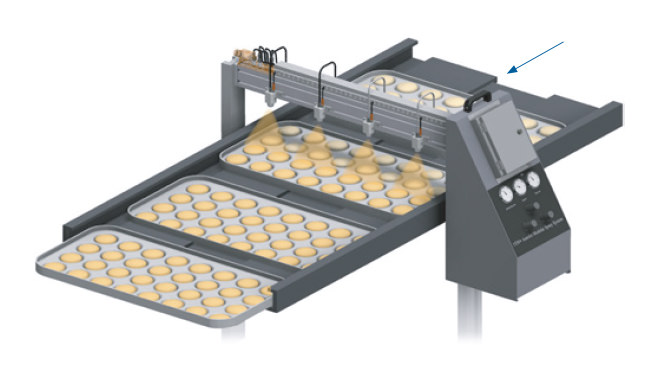
Solution:
After demonstrating the non-clogging performance of a nozzle with a larger orifice, Spraying Systems Co. installed an AutoJet® Model 1550+ Modular Spray System. The system included a 4-foot (1.2 m) 98250 spray manifold, equipped with four electrically-actuated PulsaJet® AA10000AUH spray nozzles. UniJet® self-aligning dovetail spray tips with a spray angle of 110° were used to provide complete coverage from a spray height of 10 inches (254 mm).
The AutoJet system, which integrated seamlessly with the bakery’s trigger signal and pump, provided accurate intermittent spraying of the egg wash on individual pans to minimize waste. Paramount to the system’s efficiency was Precision Spray Control (PSC), which allowed the use of larger orifices while still maintaining low flow rates (0.1 to 0.3 gallons/minute [0.4 to 1.1 liters/minute] per nozzle) to preserve pattern integrity and drop size.
Results:
By solving the bakery’s nozzle plugging problems and ensuring accurate, low-flow coverage, Spraying Systems Co. was able to reduce the bakery’s egg wash consumption by 50% and reduce the rejection rate to near zero. The constant manual labor of three employees to maintain the production line was also eliminated, saving the company substantial expense. In addition, more than 100 gallons (378.5 L) of water used for clean up each day were saved
With all of these benefits and a payback period of less than a month, the bakery’s parent company took quick notice and advised all of its bakeries running these hamburger buns to adopt the AutoJet® Model 1550+ Modular Spray System as their standard.
For complete details of this case study click here to see the PDF version.