Refinery Improves Safety & Reduces Downtime with New Cooling Quills
Refinery Improves Safety & Reduces Downtime with New Cooling Quills
Problem:
A petroleum refinery in the Midwestern US needed to cool its hydrocracker reactor prior to replacing the catalyst. A portion of the refinery was shut down to begin the cooling process. After the gas temperature decreased, a pipefitter removed a blind flange and inserted an injection quill. The quill sprayed liquid nitrogen into the reactor to continue the cooling process. This process, required every two years, caused safety concerns. The refinery wanted to eliminate the possibility of worker exposure to high-temperature hydrocarbons prior to adequate cooling. In addition, this method required a partial shutdown of the refinery and was very time consuming and costly.
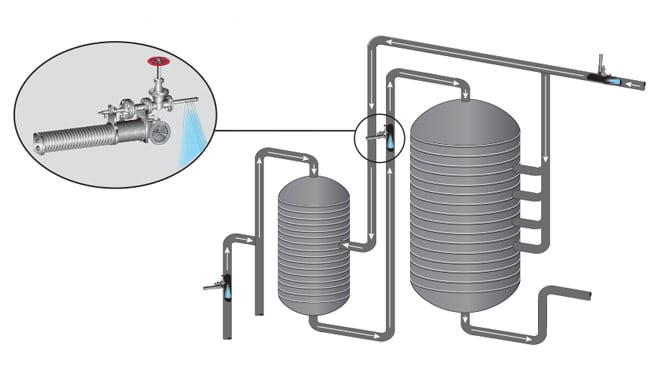
Solution:
Spraying Systems Co.’s solution consisted of using retractable quills to spray the liquid nitrogen. Computational Fluid Dynamics (CFD) modeling was used to determine how many quills were needed, where they should be installed, the spray direction and the size of the liquid orifices on each quill.
Three quills are now in use. Each quill can be mechanically inserted in the gas stream while the plant is still online, eliminating the need for a partial shutdown to begin the spray cooling process. Keeping the quills out of the gas stream between uses protects them from damage and extends usable life. The quills are compliant with the ASME® B31.3 Process Piping code and underwent positive material identification (PMI) and radiographic examination (RT) of the butt welds prior to delivery to the refinery.
Results:
The new retractable quills have helped the refinery achieve its goals of improving safety and reducing downtime. Refinery workers no longer need to insert spray quills manually, eliminating the possibility of exposure to hot gases. Hydrocracker reactor cooling time was also significantly reduced, saving the refinery two days of downtime for the catalyst replacement. With operating time at this refinery valued at US$1,000,000 per day, there was an immediate payback on the new spray equipment.
For complete details of this case study click here to see the PDF version.